Equipment and Unit Operations
From the list below, please select the "plus-box" to view corresponding information and a figure describing the selected term.
Alkaline Papermaking
Alkaline papermaking refers to the formation of paper sheets from fiber slurries having a pH generally in the range of 7 to 9. Alkaline paper sheets typically contain some form of calcium carbonate filler. Conventional acidic conditions of pH 4 to 6 cannot be used with most calcium carbonate mineral products due to dissolution of the filler and release of carbon dioxide gas. Water repellency in alkaline papermaking operations is usually achieved with synthetic sizing agents such as alkenylsuccinic anhydride or alkylketene dimer.
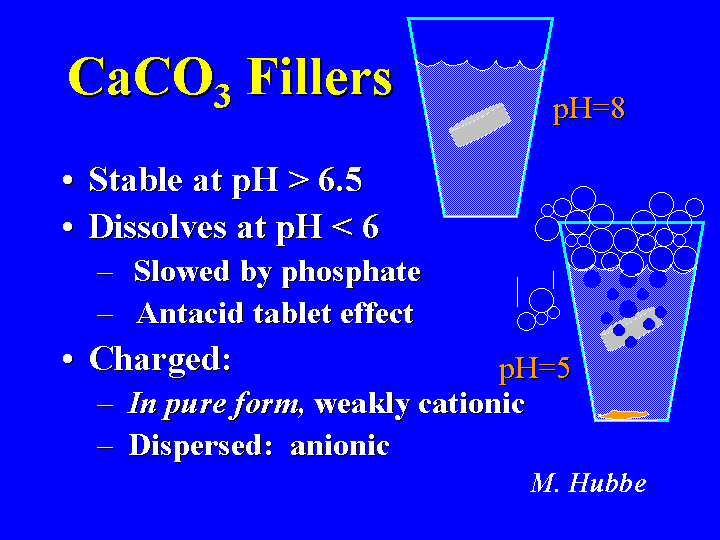
Boil-out
The purpose of a boil-out is to remove deposits of pitch, fibers, minerals, and biological slime from the wetted surfaces of a paper machine during a shutdown. The word “boil-out” has very little to do with boiling, except that the temperature within the paper machine usually is raised during a boil-out. The most common additives used during boil-out procedures are sodium hydroxide and detergents. Some mill operators alternate between alkaline boilouts and acidic boilouts. Enzymes also can be used to help release deposits from the surfaces of papermaking equipment. The frequency of boil-outs is widely variable. Some paper machines run for months without a boil-out. Others, due to chronic deposit problems, may require a boil-out within several hours of running. Effective use of retention aids, talc, and biocides has the potential to reduce the need for boiling out the paper machine as frequently.
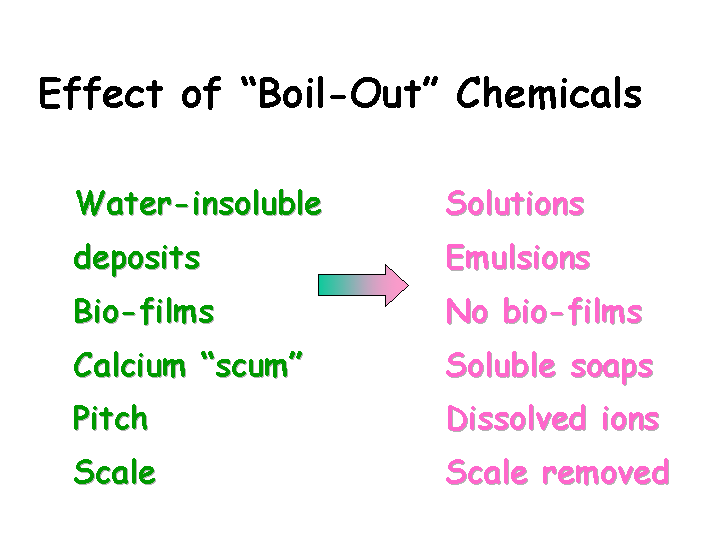
Beating (refining)
The word “beating” is often used as a synonym for “refining.” Both words refer to the passage of a fiber slurry between a rotor and stator or counter-rotating disks. Raised areas of “bars” on each surface expose the fibers to repeated compression and shearing forces. These forces gradually delaminate the fiber cell wall, increasing flexibility and fibrillation of the fiber surfaces. The expression, “paper is made in the beater,” has been passed down from the days in which most pulp was prepared batch-wise in an oblong tub with a central baffle along its lengthwise direction. Rotation of a cylinder with raised bars on its surface against a bedplate caused fiber circulation as well as refining action.
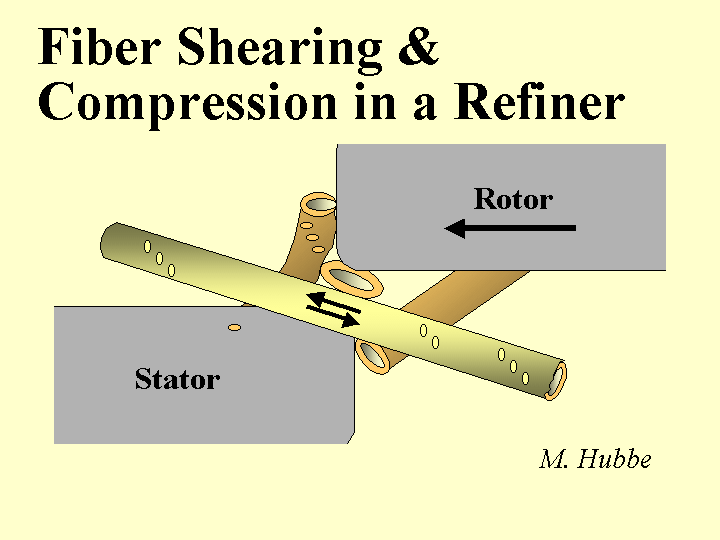
Calcining
The word “calcining” refers to treatment of a mineral product at a very high temperature such as 800 to 1000 degrees centigrade. The word is derived from the process of converting calcium carbonate to calcium oxide. This reaction plays a key role both in the production of precipitated calcium carbonate filler and in the chemical recovery cycle of kraft pulping.
When the term calcination is used together with the word “clay,” there is no calcium involved. Rather, the word “calcination” is used only because similar equipment, as used for calcium carbonate, can also be used to prepare anhydrous clay. Intense heating of kaolin clay drives off water of hydration and yields a bright, anhydrous clay product in which individual platelets of the mineral are fused together. Calcined clay is widely used in coating due to its bulking nature and brightness. Calcined clay also is abrasive. With regard to filler addition at the wet end of the paper machine, over the last 30 years economics have favored the shift from calcined clay and other clay products to calcium carbonate products.
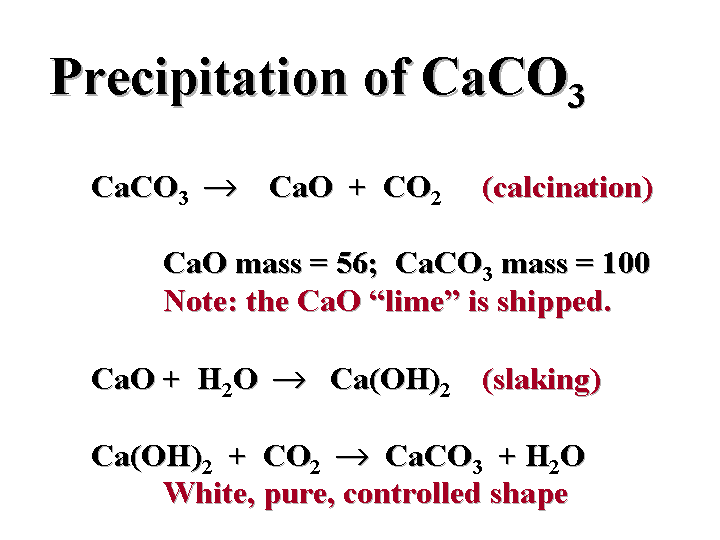
Cleaning
When papermakers use the word “cleaning” they are referring to the action of hydrocyclones. A hydrocyclone is a conical or partly cylindrical device with no moving parts, except for the fibrous slurry that flows through it. The slurry enters the hydrocyclone at a tangent along its widest part. Rapid rotation of the fluid within the hydrocyclone throws dense materials toward the outside. Conventional high-intensity forward cleaners of the type used in most paper machine systems reject the dense materials from the small end of the cone, along with about 10 to 30 percent of the flow. It is conventional practice to connect three or more banks of cleaners, using the rejects from one stage as the feed for the next. The accepts from a secondary stage of cleaning can be used as feed for the primary cleaners, etc.
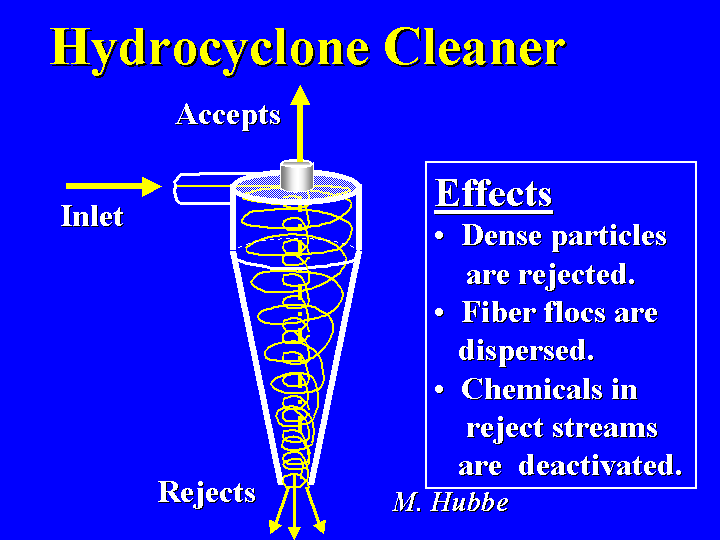
Coagulation
The word coagulation refers to the coming together and sticking of finely divided particles or droplets due to the addition of ionic materials. The principle mechanisms used to bring about coagulation are (a) neutralization of surface charges, and (b) screening of electrostatic repulsions by increasing the electrical conductivity of the solution. Coagulated dispersions or emulsions tend to settle or cream. The coagulation mechanism by itself is seldom sufficient to ensure retention of fine particles during paper manufacture. The word “flocculation” is more often used when one is referring to treatment with retention aids that are capable of forming shear-resistant bonds between fine particles, fiber-fines, and fibers.
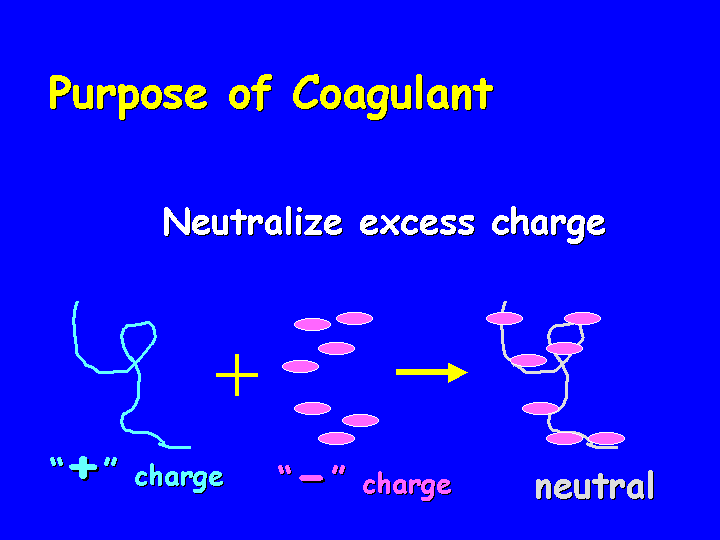
Couch
The function of couch roll (pronounced “cooch”) of a paper machine is to remove water by application of vacuum. It also serves as the final “wrap” where the wet web exits the forming fabric on its way to the wet-press section. The surface of the couch roll is covered with rows of small holes. Baffles within the interior of the couch roll direct the vacuum toward that segment of the roll where the wet web is on the fabric. Unlike vacuum boxes, an increase in vacuum does not increase the power needed to drive the forming fabric. However, too high an application of vacuum at the couch is likely to produce visible suction-hole “shadows” due to movement of fines within the sheet.
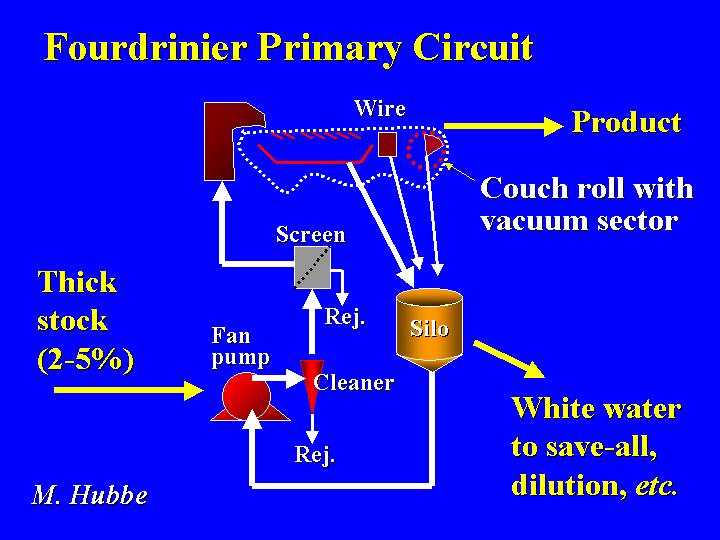
Dragging the Sheet
Papermakers use the word “dragging” to describe the situation in which a forming fabric is moving faster than the jet of stock coming from the slice. On many paper machines a minor amount of drag, say 1-3%, can improve formation uniformity. Dragging also tends to give fibers a preferential alignment in the machine direction. As a consequence, the machine-directional strength properties are expected to be higher than the cross-directional properties. The opposite of dragging is rushing.
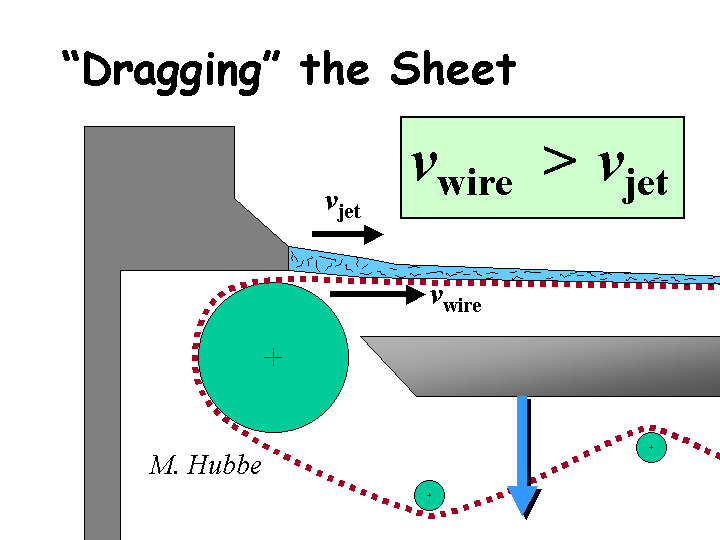
Drainage and Dewatering
The words “drainage” and “dewatering” refer to the removal of water from the wet web during the formation of paper. Sometimes papermakers refer to “gravity drainage,” i.e. the removal of water without use of vacuum. The action of hydrofoils is usually considered to fall within the heading of gravity drainage. The more general term “dewatering” includes not only gravity drainage, but also the effects of vacuum boxes, the couch roll, and wet-pressing. Chemical factors that increase dewatering by gravity do not necessarily achieve an overall benefit, since the effectiveness of vacuum dewatering is highly dependent on the uniformity of the paper. Fiber flocs or pin-holes in paper can make vacuum dewatering less effective.
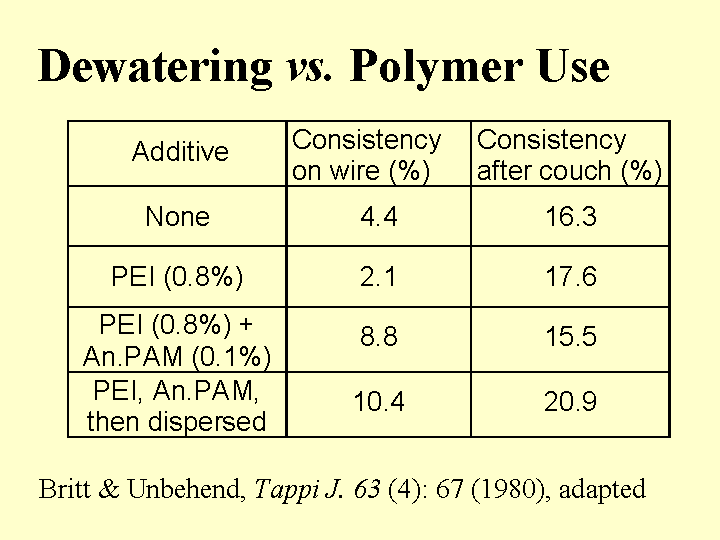
Fan Pump
The fan pump propels the dilute slurry of papermaking furnish towards the headbox of a paper machine. The pumps are designed in such a way as to minimize pulsation, since the goal is to keep the basis weight constant over time and avoid “barring”. Thick stock, often having a consistency of about 3 to 5% is diluted with white water at the inlet of the fan pump. The consistency of thin-stock furnish coming out of the fan pump is typically between 0.3% and 1% solids. Papermakers often add chemicals such as fillers, acid, or base before the fan pump so that they can take advantage of the mixing action. Fan pumps are typically located in the basement underneath the forming section of the paper machine. Some paper machines employ two separate fan pumps so that it is possible to optimize the performance of hydrocyclone cleaners, with or without subsequent deaerating equipment.
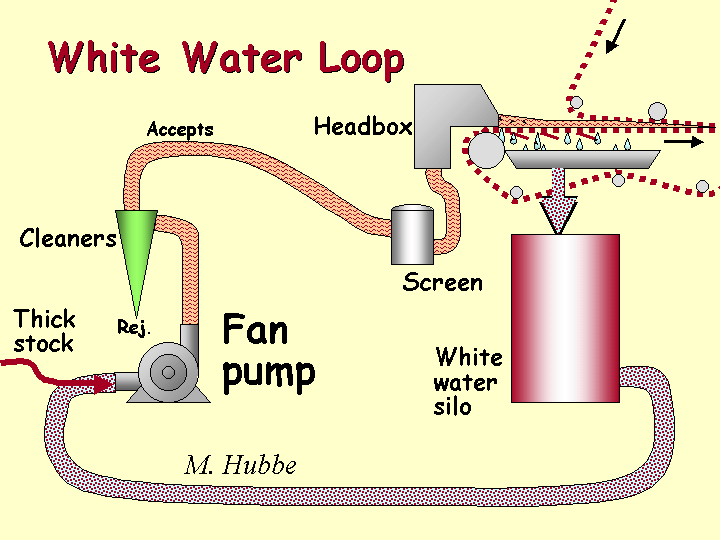
Flocculation
The word flocculation has two meanings. When used by colloidal chemists, the word implies a process by which either colloidal materials or other suspended materials are brought together by the action of high-mass polyelectrolytes. Usually the term flocculation implies a mechanism in which polyelectrolytes bridge between the suspended particles or fibers. When used by papermakers, the word flocculation also can mean the grouping of fibers into bunches that have enough strength to persist after flow is stopped. Flocculation occurs in shear flow due to the fact that wood fibers have a length-to-thickness ratio of about 50 to 100. The action of charge-neutralizing additives such as alum or polyamines tends to increase fiber flocculation by a modest amount. Severe flocculation can be caused by excessive use of very high-mass polyelectrolytes, i.e. retention aids.
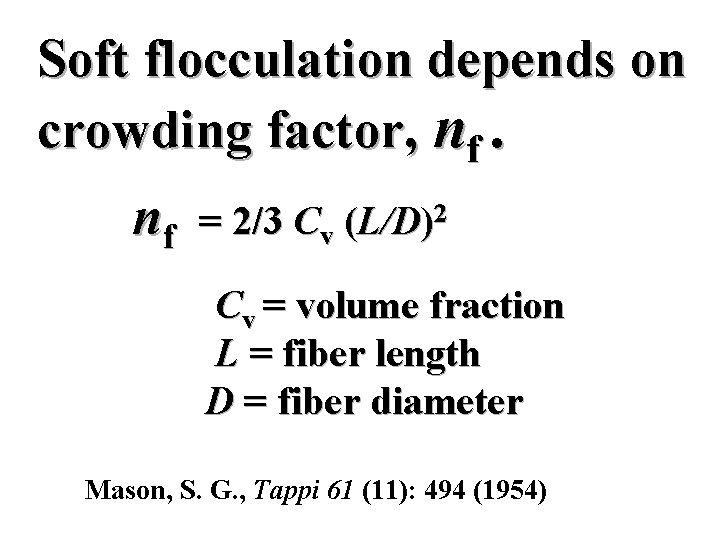
Foils (hydrofoils)
The function of hydrofoils (“foils” for short) is to aid in removal of water from a wet web in the early stages of dewatering. On a Fourdrinier paper machine the foils are placed under the forming fabric. Their shape is designed to create suction as the foil and wet web pass over the surface. Hydrofoils also create a brief pressure pulse as the fabric passes over the leading edge. The alternating pressure and vacuum of a series of hydrofoils tends to move fibers around in the wet web, slightly improving the drainage and uniformity of the resulting paper. Also, the pulsation tends to change the drainage mechanism from pure filtration to a combination of filtration and thickening. The washing action of hydrofoils tends to remove fiber fines and fillers from the wire side(s) of a paper sheet. Another function of the hydrofoil is to doctor water from the under-side of the forming fabric.
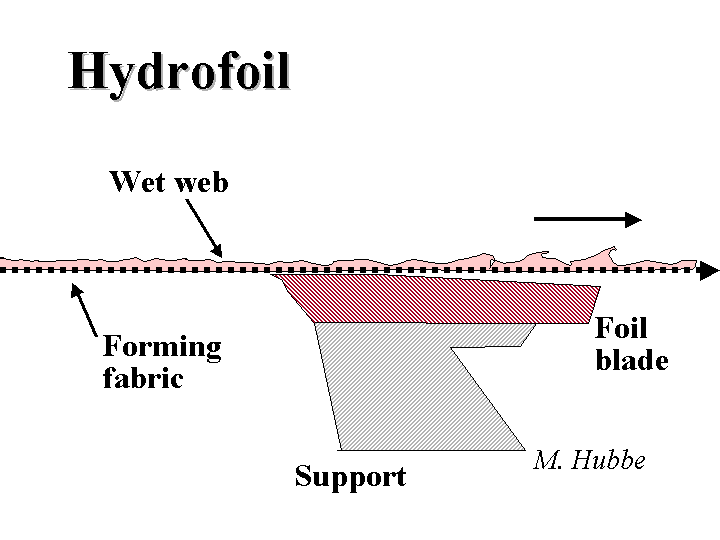
Forming
Papermakers use the word “forming” to describe the process in which a slurry of fibers having a solids level of 0.3 to 1% is converted into a wet web having a solids level of about 15 to 22%. Forming is accomplished with a variety of equipment. The most traditional equipment is the single-fabric Fourdrinier paper machine. On a Fourdrinier machine a wide jet of dilute furnish is applied from a headbox onto the surface of a continuously moving wire screen. Water is removed by gravity and with the help of hydrofoils (or alternatively, table-rolls), vacuum boxes, and vacuum applied at the couch roll. A dandy roll (screen cylinder) or a top-wire may be used to make the sheet more uniform. Twin-wire machines (gap formers) employ two continuously moving fabrics and the jet of furnish is directed into the closing gap. This format tends to produce a sheet that is symmetrical in the z-direction.
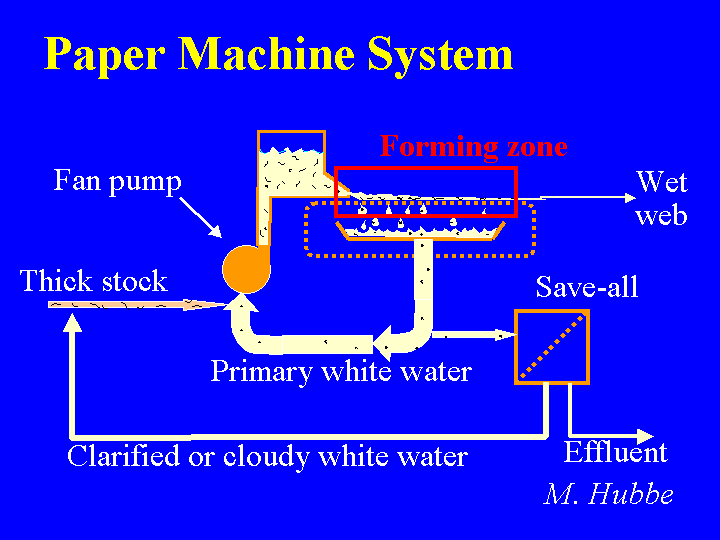
Forming Fabric
The forming fabric or “wire” of a paper machine is the continuous belt or belts of mesh screen upon which the paper sheet is formed. Most modern forming fabrics are no longer comprised of metal wires. Rather, they are comprised of monofilament plastic strands. The weave pattern and layering of a forming fabric is designed to meet stringent requirements of dimensional stability, resistance to abrasion (on the wire side), minimum resistance to drainage, minimum wire-mark, and (sometimes) maximization of retention of fiber fines. Traditional Fourdrinier paper machines have a single wire. Modified Fourdriniers and gap formers can have two.
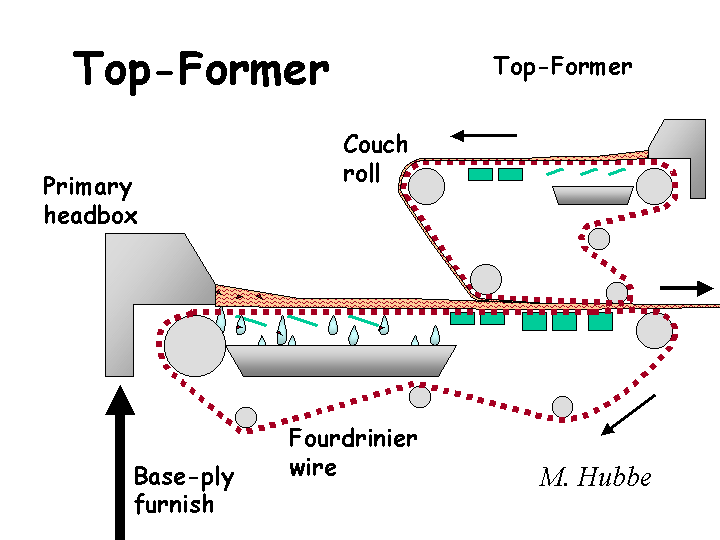
Fourdrinier
The most traditional paper-forming equipment is the single-forming-fabric Fourdrinier paper machine. On a Fourdrinier machine a wide jet of dilute furnish is applied from a headbox onto the surface of a continuously moving wire screen. Water is removed by gravity and with the help of hydrofoils (or alternatively, table-rolls), vacuum boxes, and vacuum applied at the couch roll. A dandy roll (screen cylinder) or a top-wire may be used to make the sheet more uniform. The name Fourdrinier has been passed down from the English entrepreneurs who first commercialized the continuous forming machine invented by Louis Robert.
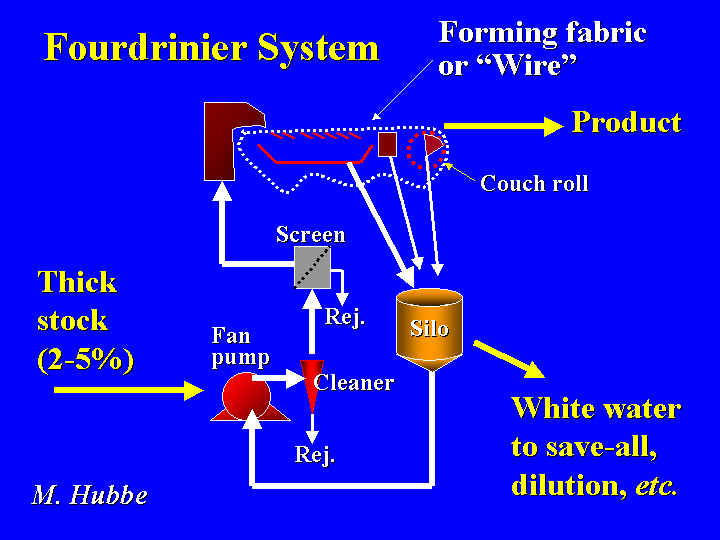
Gap Former
In a twin-wire paper forming machine or “gap-former” the jet of furnish from the headbox is directed into the narrowing gap between two forming fabrics. Water is removed in both directions. The rate of water removal may be enhanced by passing the pair of forming fabrics around a roll, over blades, or over vacuum elements. The bi-directional removal of water tends to produce a sheet in which the fines content and appearance of the two sides is very similar. Because the sheet becomes “set” very rapidly within a gap former, the uniformity of furnish emerging from the headbox can be critical.
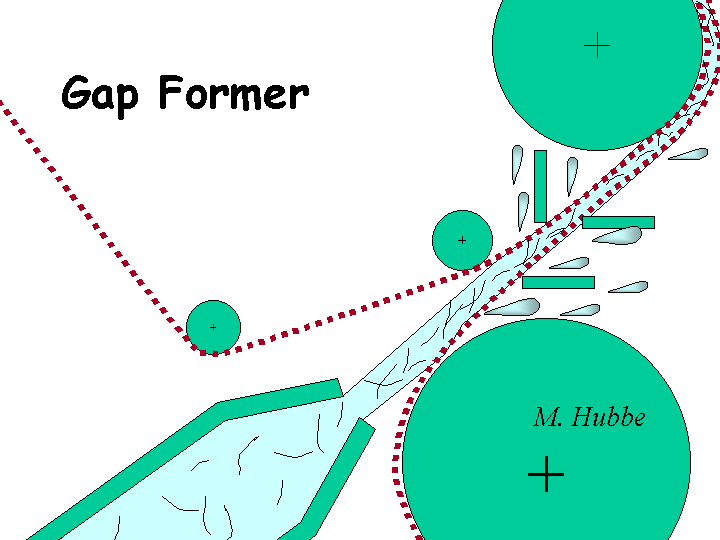
Graniting
Papermakers use the word “graniting” to refer to a speckled appearance of paper, especially in cases where dyes have been added. Graniting may be caused when high-affinity dyes are allowed to contact furnish or white water at relatively high concentration or with inadequate mixing. The solids at the point of dye addition become irreversibly stained and remain deeper in shade than the rest of the furnish. Graniting usually can be reduced by dilution of the dye with solids-free water before it is added to the furnish. Also it is recommended to add high-affinity dyes to points in the process where there is good mixing. Graniting may also occur if dyes are allowed to contact oppositely charged materials before they have become well mixed with the furnish.
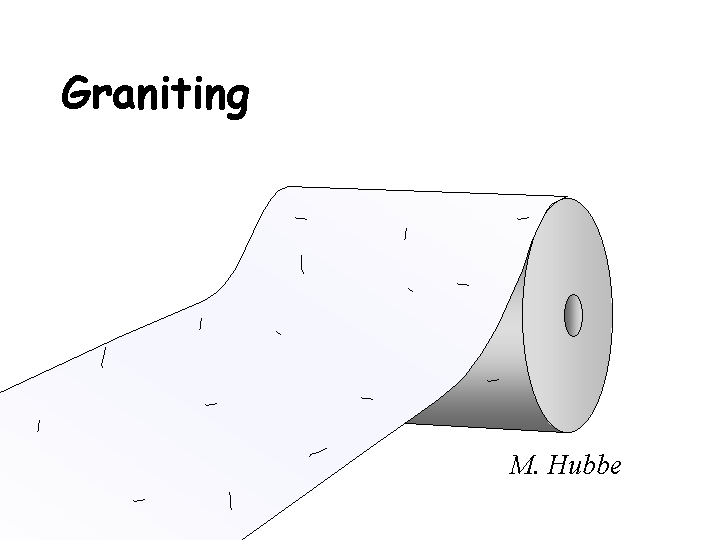
Headbox
The function of a headbox is to deliver a uniform jet of furnish having essentially the same width as the paper web to be produced. The word is derived from earlier days when the hydrostatic head within the box was sufficient to deliver a jet velocity to approximately match the speed of the forming fabric. Except in rare instances, those days are long gone. Rather, the pressure within a modern headbox is maintained by pumps and controls. Air-padded headboxes use an air-space above the furnish as a means of controlling the pressure. Rectifier rolls (or “holey rolls”) are cylinders with large holes in them, slowly rotating within an air-padded headbox to help distribute the furnish and prevent deposition of materials. Hydraulic headboxes have neither air spaces nor rectifier rolls. Redistribution of furnish and break-up of flocs is achieved with banks of tubes, expansion areas, and changes of flow direction.
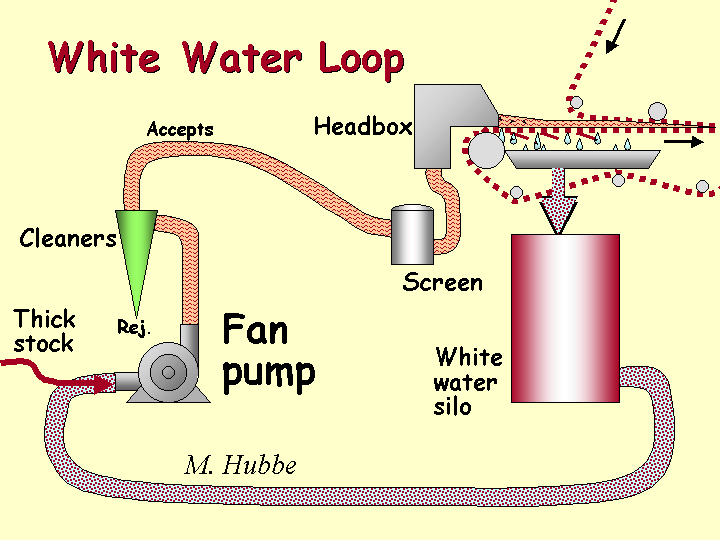
Hydrocyclone (cleaner)
When papermakers use the word “cleaning” they are referring to the action of hydrocyclones. A hydrocyclone is a conical or partly cylindrical device with no moving parts, except for the fibrous slurry that flows through it. The slurry enters the hydrocyclone at a tangent along its widest part. Rapid rotation of the fluid within the hydrocyclone throws dense materials toward the outside. Conventional high-intensity forward cleaners of the type used in most paper machine systems reject the dense materials from the small end of the cone, along with about 10 to 30 percent of the flow. It is conventional practice to connect three or more banks of cleaners, using the rejects from one stage as the feed for the next. The accepts from a secondary stage of cleaning can be used as feed for the primary cleaners, etc.
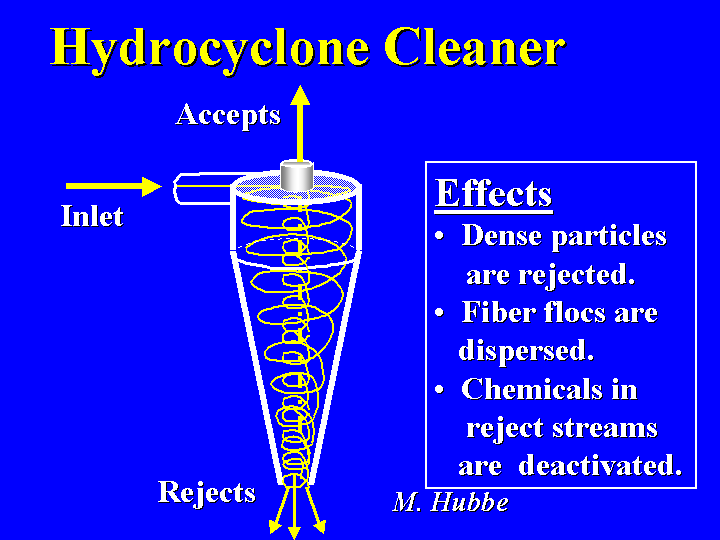
Hydrolysis
The word “hydrolysis” implies a reaction of something with water. A well-known example is the reaction between alkenylsuccinic anhydride (ASA) sizing emulsions and water. The product of such a reaction is a hydrolyzate.
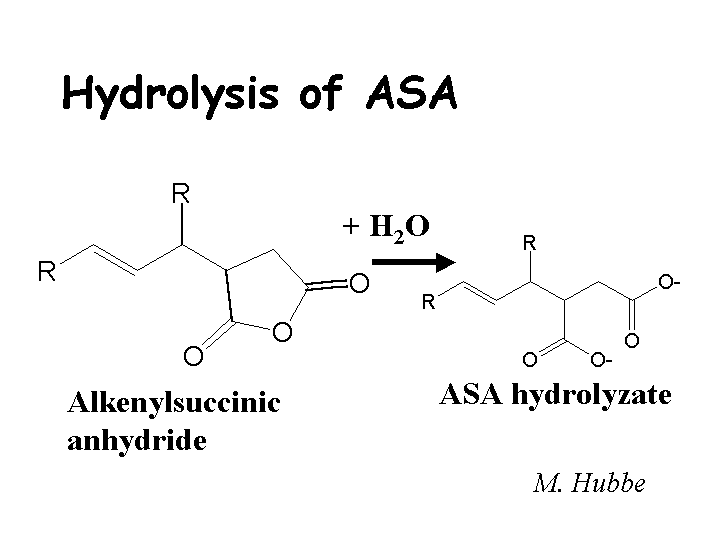
Hydrofoil
The function of hydrofoils (“foils” for short) is to aid in removal of water from a wet web in the early stages of dewatering. On a Fourdrinier paper machine the foils are placed under the forming fabric. Their shape is designed to create suction as the foil and wet web pass over the surface. Hydrofoils also create a brief pressure pulse as the fabric passes over the leading edge. The alternating pressure and vacuum of a series of hydrofoils tends to move fibers around in the wet web, slightly improving the drainage and uniformity of the resulting paper. Also, the pulsation tends to change the drainage mechanism from pure filtration to a combination of filtration and thickening. The washing action of hydrofoils tends to remove fiber fines and fillers from the wire side(s) of a paper sheet. Another function of the hydrofoil is to doctor water from the under-side of the forming fabric.
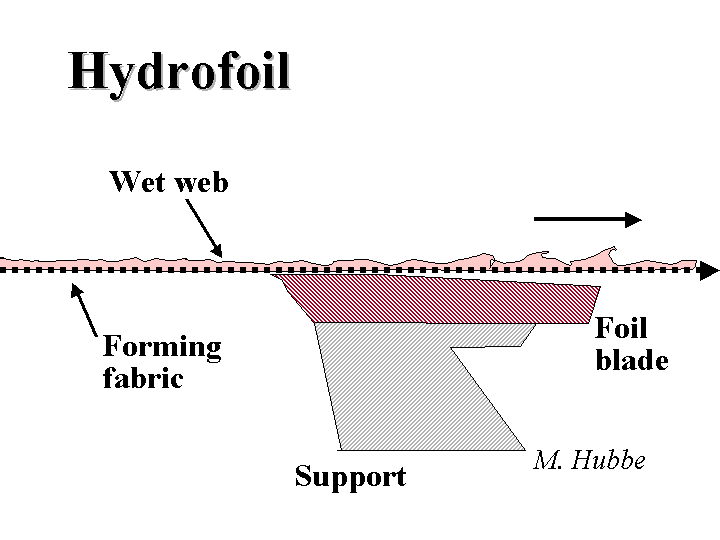
Inversion of an Emulsion
An emulsion is “inverted” when the dispersed phase becomes the continuous phase and vice versa. High-mass acrylamide retention aid products are often prepared and shipped as water-in-oil emulsions. Successful make-down of such an emulsion requires a high degree of dilution (e.g. 200-to-1) and well-controlled hydrodynamic shear. The oil droplets released by inversion of a retention aid emulsion usually are retained harmlessly in the paper product. Problems with inversion of a retention aid emulsion are likely to result in fish-eyes, partly solubilized gels of polymer.
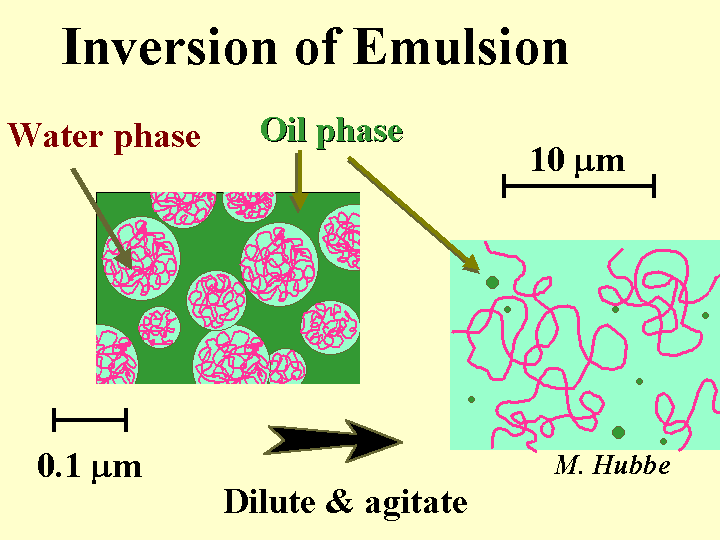
Pressure Forming
The words “pressure forming” refer to the angle at which the jet of furnish from a headbox slice impinges upon the forming fabric near to a breast roll or forming board. In the case of pressure forming the angle is relatively steep, driving the jet toward the fabric. Pressure forming tends to set a mat of fibers against the surface of the forming fabric very quickly, possibly “sealing the sheet” (impeding further drainage). Pressure forming is sometimes used to achieve a desired sheet structure or break up fiber flocs. The opposite of pressure forming is “velocity forming,” in which the jet is laid almost parallel onto the forming fabric. Velocity forming tends to favor good drainage performance and retention.
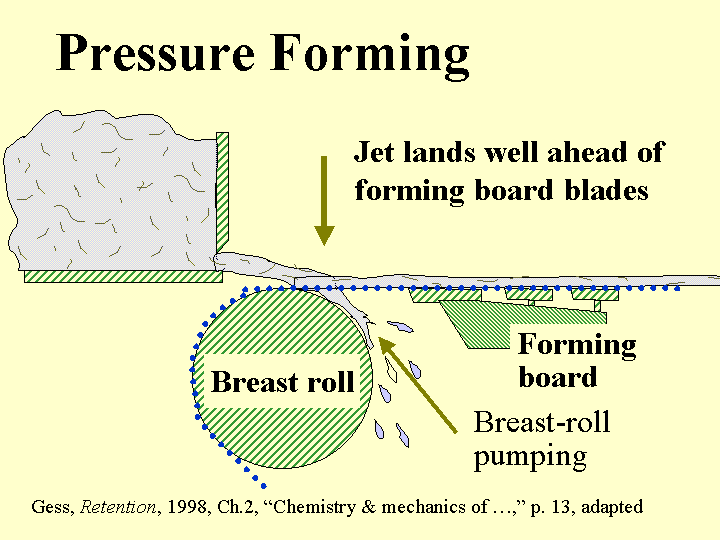
Pressure-Screen
The function of a pressure screen in a paper machine thin-stock recirculation system is to remove shives (fiber bundles) and other large, hard contaminants from the furnish. Conventional pressure screens use baskets with either slots or holes to admit the fibrous “accepts” flow and reject the contaminants. Slotted screens usually have a sculptured pattern that helps fibers to become aligned and pass through the screen. Pressure screens are equipped with various types of rotors to continuously redisperse any fibers that start to accumulate on the screen surface. Because fibers can pass through a slotted screen individually, but not as fiber flocs, papermakers sometimes choose to add retention aids ahead of pressure screens in order to achieve a favorable balance of formation uniformity and adequate retention of fine particles
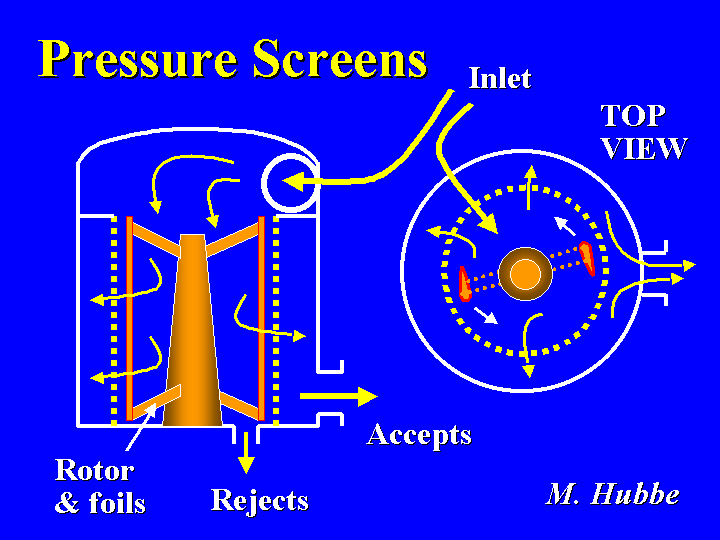
Quill
Papermakers sometimes use the word “quill” when referring to pipe assemblies that discharge papermaking chemical solutions into the interior flow of fiber furnish within stock lines (large pipes). The purpose of a quill is to maximize mixing of the additives with fibers and minimize the chance of deposition on the walls of the stock line. Chemicals added with a quill tend to become adequately mixed over a wide range of pre-dilution. The cross-tubes or other structures used for quill injection are a potential site for accumulation of strings of fibers that later may break off and get into the product. Over time the surfaces of quill equipment tend to become polished due to the abrasive action of the furnish. It has been suggested that severe abrasion may eventually cause quill parts to come loose and damage other parts of the paper machine.
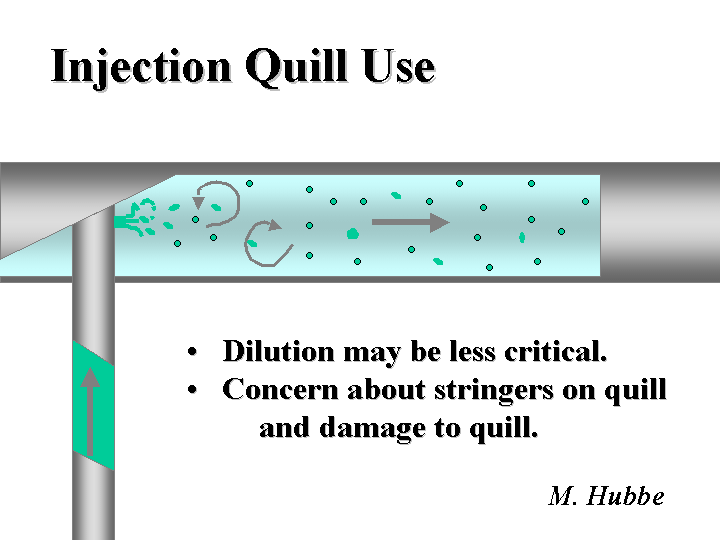
Rectifier Roll
The rectifier roll is an empty stainless steel cylinder with large holes in its surface. Papermakers often refer to rectifier rolls as “holey rolls.” The rectifier rolls rotate at a controlled rate below the water-line of an air-padded headbox. The function of a rectifier roll is to even out to flow of fibers within the headbox and prevent settling. The speed of rotation can be optimized to minimize defects such as barring (periodic MD-variations in weight) and flocs associated with the holes in the rectifier rolls.
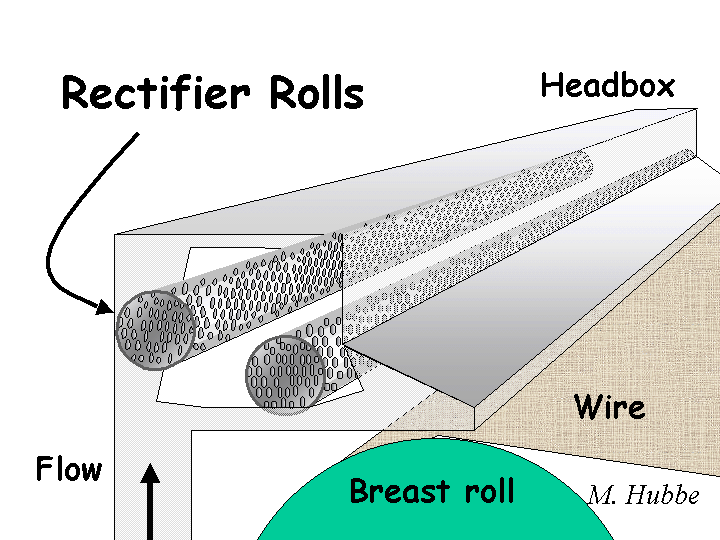
Refining (beating)
The word “beating” is often used as a synonym for “refining.” Both words refer to the passage of a fiber slurry between a rotor and stator or counter-rotating disks. Raised areas of “bars” on each surface expose the fibers to repeated compression and shearing forces. These forces gradually delaminate the fiber cell wall, increasing flexibility and fibrillation of the fiber surfaces. The expression, “paper is made in the beater,” has been passed down from the days in which most pulp was prepared batch-wise in an oblong tub with a central baffle along its lengthwise direction. Rotation of a cylinder with raised bars on its surface against a bedplate caused fiber circulation as well as refining action.
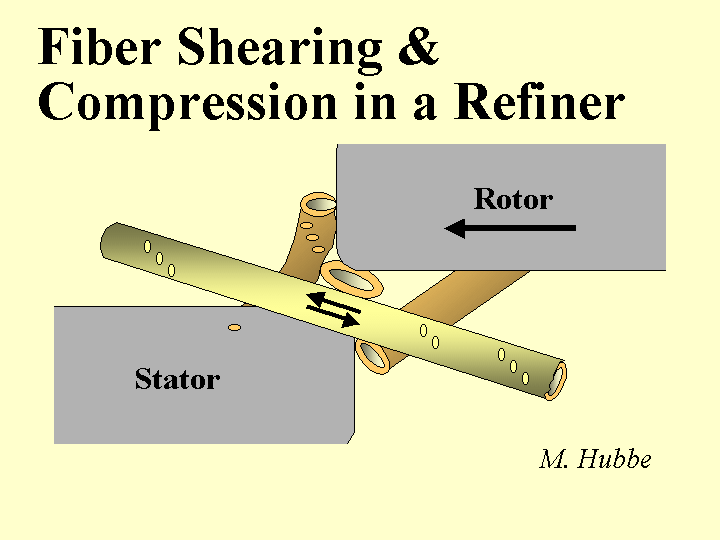
Reptation
Reptation refers to the diffusion of a high-mass soluble polymer into a pore that has a characteristic size smaller than the polymer’s average conformation in solution. Over time the polymer may be able to work its way into the pore “single file,” starting at one end. The process of reptation tends to be inhibited by high molecular mass, branched polymer structures, or very high affinity between polymer segments and the substrate. There is evidence that polymers of molecular mass lower than about 10,000 grams per mole are able to reticulate into the pores in the cell walls of kraft fibers.

Rushing the Sheet
Papermakers use the word “rushing” to describe the situation in which the forming fabric is moving slower than the jet of stock. On many paper machines a minor amount of rush, say 1-3% relative to the fabric velocity, can improve formation uniformity. Rushing also tends to give fibers a greater alignment in the z-direction than they would have otherwise. Excessive rushing of a sheet is expected to hurt product strength and reduce the uniformity of formation. The opposite of rushing is dragging.
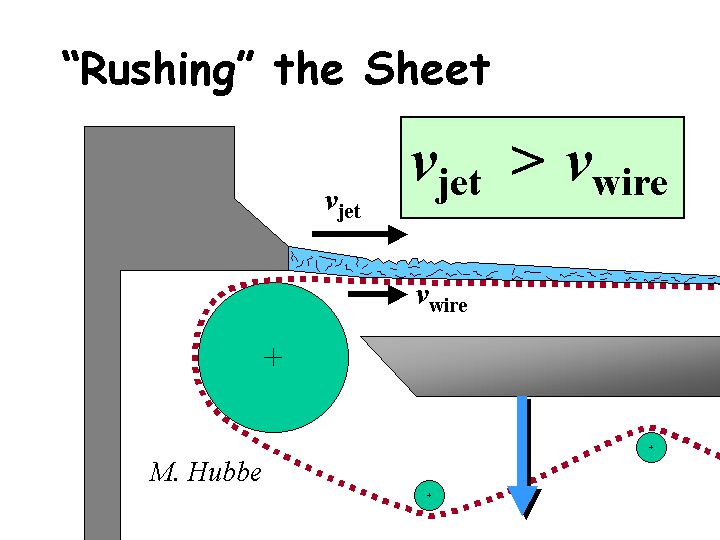
Saponification
The word “saponification” implies conversion of something into its corresponding soap form, i.e. the sodium salt of an acid. Rosin acid emulsion products may become saponified if they are allowed to remain in contact with stock for a long time, as in the case of poor first-pass retention. Saponification reactions are favored by increasing pH, temperature, and time. Many components of wood pitch may become saponified under alkaline papermaking conditions. Even the nonionic triglyceride portion of wood pitch can be saponified, especially at very high pH or in the presence of enzymes. Components of pitch that have no ester groups or carboxylic acid groups are known as “unsaponifiables.”
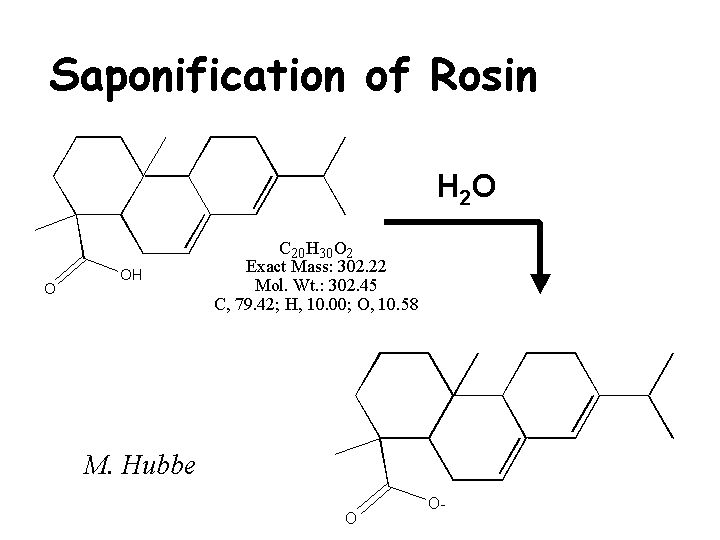
Save-All
The function of a save-all is to remove fiber fines and other solids from white water. The clarified white water can then be used for showers, for stock dilution, and for make-down of certain types of chemical product. Also it can be stored with a much-reduced chance of materials becoming settled as deposits. Clarified white water from a save-all also may be discharged to wastewater treatment, minimizing the loss of solids from the process. The most widely used types of save-alls use disk screens or drum screens. Some long fiber or broke usually is added to aid in the filtration of fines. Dissolved-air-flotation (DAF) equipment is also used for flotation save-alls in many mills. Such processes are designed so that fiber fines and other solids rise to the top of a shallow chest where they can be skimmed off and recovered.
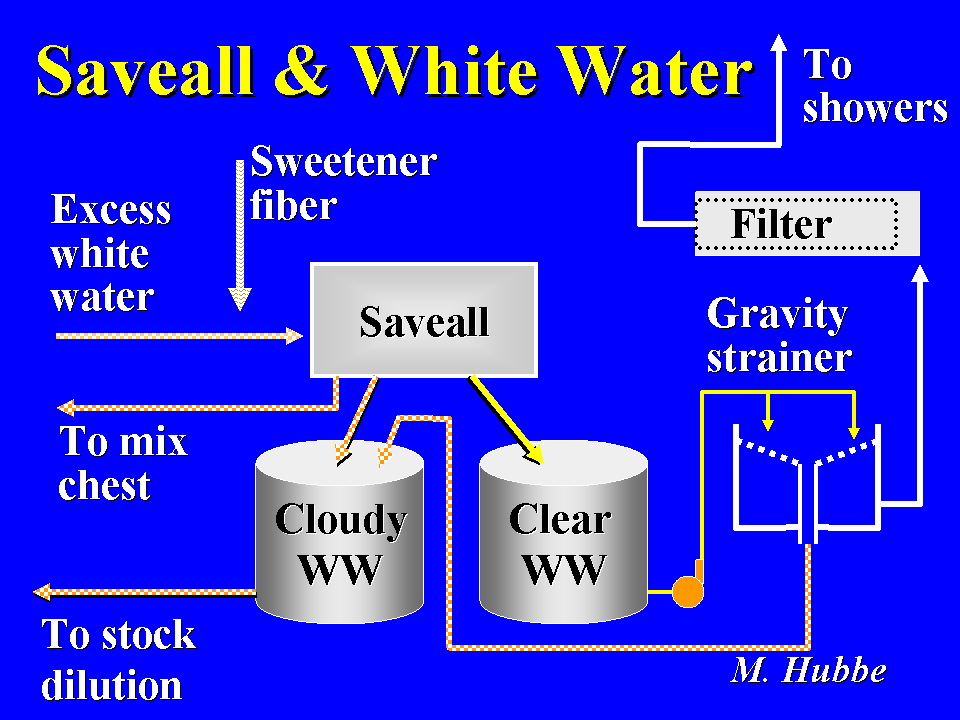
Screen (pressure-screen)
The function of a pressure screen in a paper machine thin-stock recirculation system is to remove shives (fiber bundles) and other large, hard contaminants from the furnish. Conventional pressure screens use baskets with either slots or holes to admit the fibrous “accepts” flow and reject the contaminants. Slotted screens usually have a sculptured pattern that helps fibers to become aligned and pass through the screen. Pressure screens are equipped with various types of rotors to continuously redisperse any fibers that start to accumulate on the screen surface. Because fibers can pass through a slotted screen individually, but not as fiber flocs, papermakers sometimes choose to add retention aids ahead of pressure screens in order to achieve a favorable balance of formation uniformity and adequate retention of fine particles.
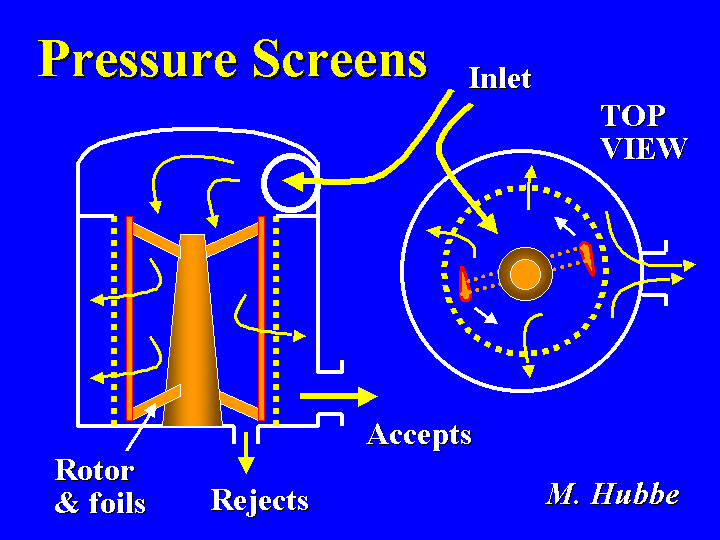
Silo (whitewater silo)
When papermakers use the term “silo” they are usually referring to a white water chest within the primary flow circuit of a paper machine. The function of a silo is to provide substantially bubble-free water to the fan pump. The idea is that bubbles larger than a critical size will rise rapidly enough to stay ahead of the current, reach the surface, and pop. Often it is necessary to use an adequate amount of defoamer chemical so that very small bubbles coallesce into larger bubbles. The silo also provides sufficient volume such that there is always enough water to respond to momentary changes in the demand for dilution water.
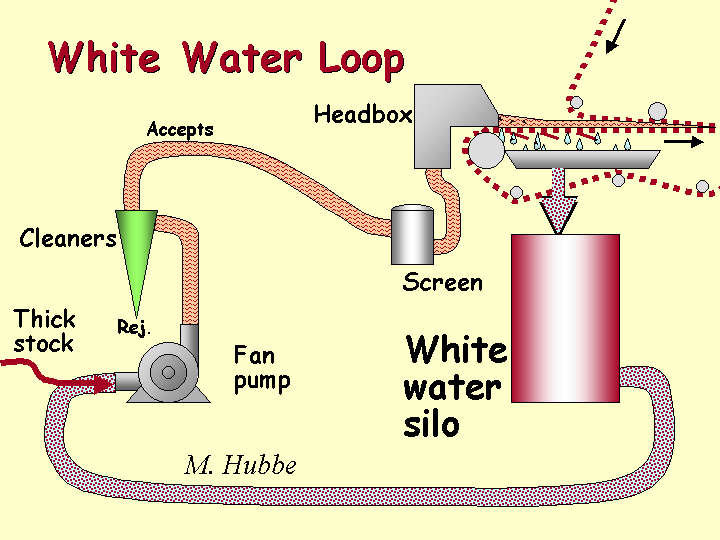
Sizing
When papermakers use the word “sizing” it is sometimes a good idea to ask whether they are referring to internal (wet-end) sizing or surface sizing (at a size press). The function of internal sizing is to increase the resistance to liquid penetration into or through paper. This effect can be achieved under acidic papermaking conditions with rosin and alum. Under alkaline papermaking conditions it is common to use alkenylsuccinic anhydride (ASA) or alkylketene dimer (AKD) for internal sizing. The principle function of surface sizing usually is to strengthen the surface of the sheet with a discontinuous film of inexpensive starch. Some papermakers also add to water resistance by adding hydrophobic polymers such as styrenemaleic anhydride (SMA), styrene acrylate (SA), or alkylated urethane polymers to the sizes press starch solution.
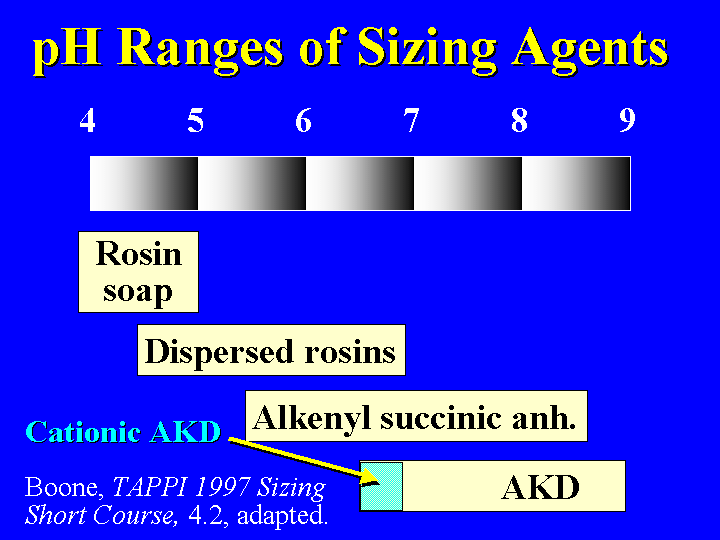
Slaking
The word slaking means the addition of water to calcium oxide powder (lime). The resulting product is calcium hydroxide (milk of lime). The reaction is exothermic, so the mixture heats up. Slaking is a key step in the most widely used procedure for formation of precipitated calcium carbonate. Slaking is also used as part of the chemical recovery cycle for the kraft pulping process.
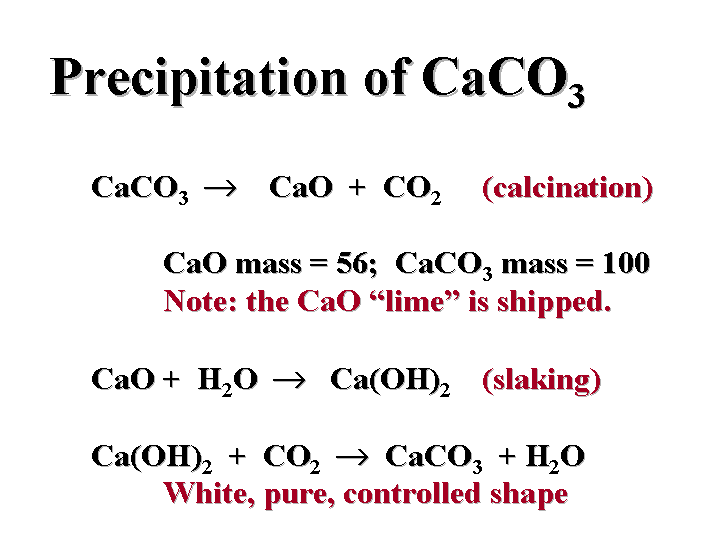
Slice
The slice is a slit-like opening in a headbox from which a jet of dilute fiber furnish emerges and then lands on the forming fabric. Papermakers can control the width of the slice opening to adjust such parameters as the jet speed, the basis weight profile, and the amount of dilution water added at the fan pump. They also can adjust the relative positions of the opening and a protruding lower lip of the slice. Such adjustments will affect the angle at which stock strikes the forming fabric, making it possible to practice pressure forming, velocity forming, or intermediate forming conditions. Chemical-related deposits on either slice lip can have a major adverse effect on product uniformity, creating wake effects and associated machine-directional streaks in the product.
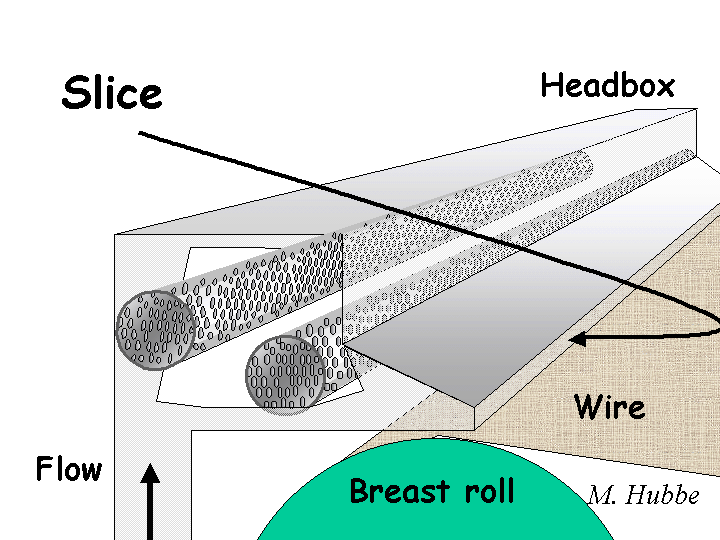
Stuff Box
The function of a stuff box is to provide a constant head of thick-stock furnish to be metered into the fan pump. It is critical that the thick-stock valve always perform with high accuracy and predictability. As shown in the picture, an excess of stock from a machine chest is pumped upwards into the base of a stuff box. Part of the flow passes over a weir and drops by gravity through pipes leading back to the machine chest. Another part of the flow satisfies the demand of the thick-stock valve and fan pump. Because of its easy accessibility, the stuff box is often used as the addition point for chemicals.
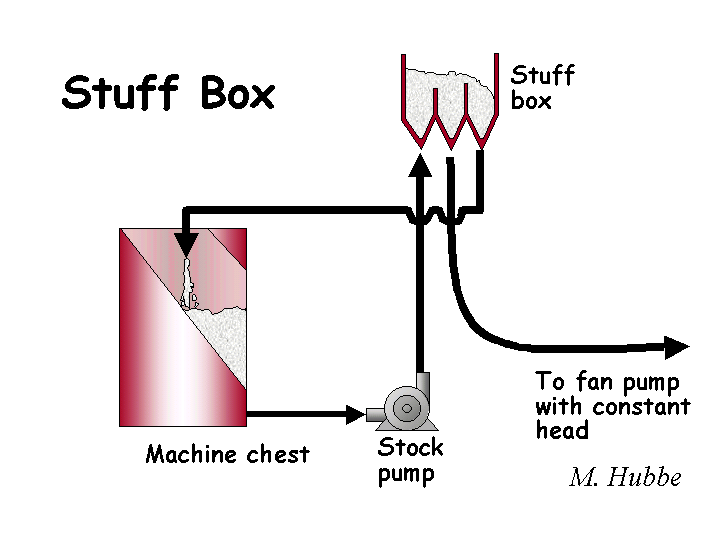
Top-Former
Fourdrinier machines may be modified with the addition of a top-wire dewatering unit, making it possible to produce a sheet with greater symmetry and much better dewatering. The next further step in sophistication is to place a headbox and dewatering elements on the top unit, making it into another Fourdrinier former. The two sheets are joined together when the forming fabrics come together. Some paper machines are set up with separate stock systems for different headboxes, making it possible to use premium fibers or other materials in a top ply.
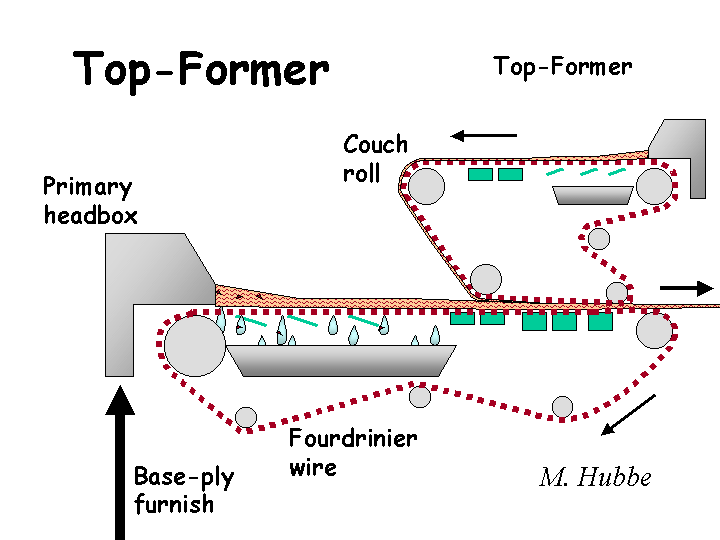
Tray
The tray of a paper-forming machine is the collection point for white water that drains from the wet web before any application of vacuum. The tray is often filled with foam, punctuated by the “rain” of white water coming from hydrofoils. Tray water typically has a higher fines concentration when compared to the lesser amounts of white water collected from vacuum boxes, the couch roll, and wet presses. Modern systems for control of retention aid flows require accurate measurement of tray water solids. This can be a difficult number to obtain with accuracy due to the tendency of foam bubbles to float some of the fine materials, and due to the fact that the early parts of the dewatering process yield white water that is much richer in fines than the later parts. The greater clarity of white water farther down the paper machine is due to the filtering effect of the wet web itself.
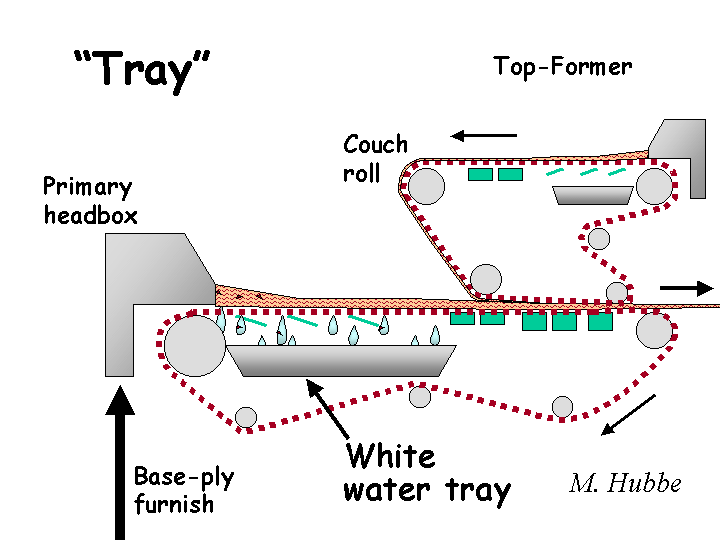
Twin-wire former
In a twin-wire paper forming machine or “gap-former” the jet of furnish from the headbox is directed into the narrowing gap between two forming fabrics. Water is removed in both directions. The rate of water removal may be enhanced by passing the pair of forming fabrics around a roll, over blades, or over vacuum elements. The bi-directional removal of water tends to produce a sheet in which the fines content and appearance of the two sides is very similar. Because the sheet becomes “set” very rapidly within a gap former, the uniformity of furnish emerging from the headbox can be critical.
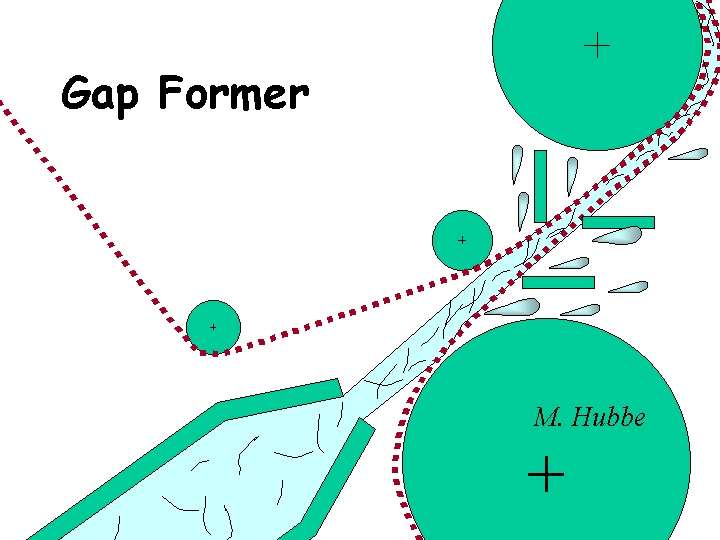
Velocity Forming
The words “velocity forming” refer to the angle at which the jet of furnish from a headbox slice impinges upon the forming fabric near to a breast roll or forming board. In the case of velocity forming the angle is relatively shallow, laying the jet gently on the fabric. Velocity forming tends to favor good drainage performance and retention. However, a sheet that emerges from the slice in a flocculated condition will not be improved in formation uniformity by velocity forming. The opposite of velocity forming is pressure forming. Pressure forming tends to set a mat of fibers against the surface of the forming fabric very quickly, possibly “sealing the sheet” (impeding further drainage). Pressure forming is sometimes used to achieve a desired sheet structure or break up fiber flocs.
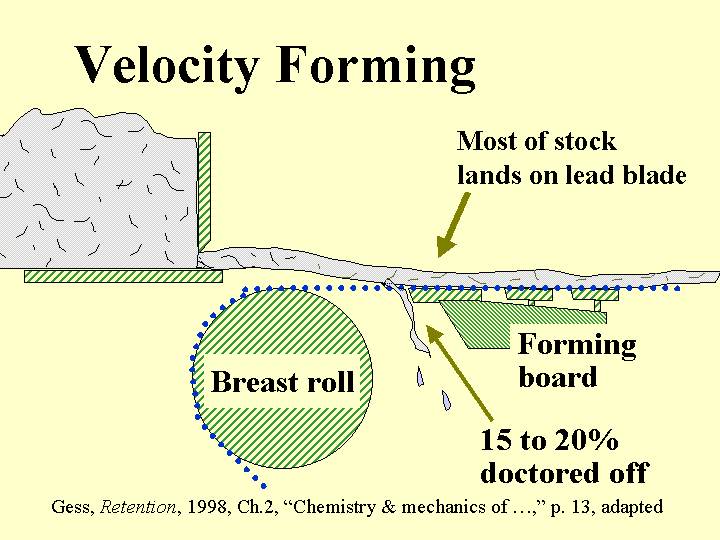
Wire (forming fabric)
The forming fabric or “wire” of a paper machine is the continuous belt or belts of mesh screen upon which the paper sheet is formed. Most modern forming fabrics are no longer comprised of metal wires. Rather, they are comprised of monofilament plastic strands. The weave pattern and layering of a forming fabric is designed to meet stringent requirements of dimensional stability, resistance to abrasion (on the wire side), minimum resistance to drainage, minimum wire-mark, and (sometimes) maximization of retention of fiber fines. Traditional Fourdrinier paper machines have a single wire. Modified Fourdriniers and gap formers can have two.
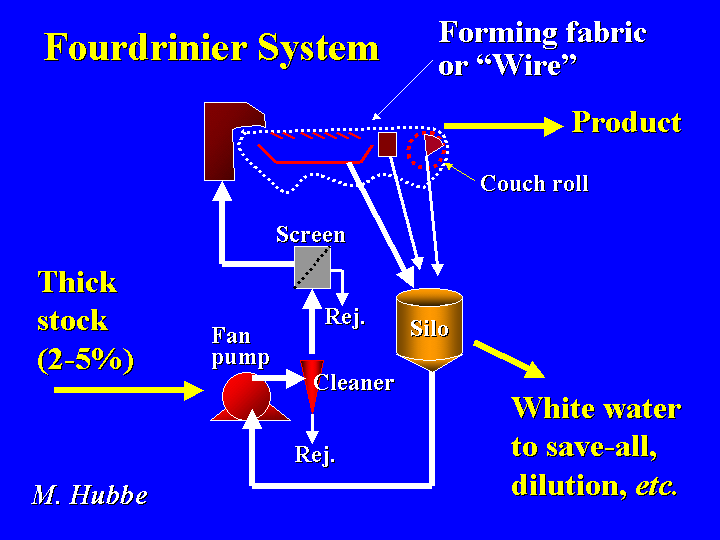