Definitions and concepts
The accordion list below provides basic information about a range of definitions and concepts in papermaking wet-end chemistry.
Acidity (total acidity)
The acidity or “total acidity” of an aqueous mixture equals the amount of strong base (such as NaOH) required to raise the pH of a unit volume or mass of sample to a value of 8.3. In general we cannot estimate a sample’s total acidity by knowing its pH. Mixtures that contain weak acids such as alum tend to have high values of total acidity.
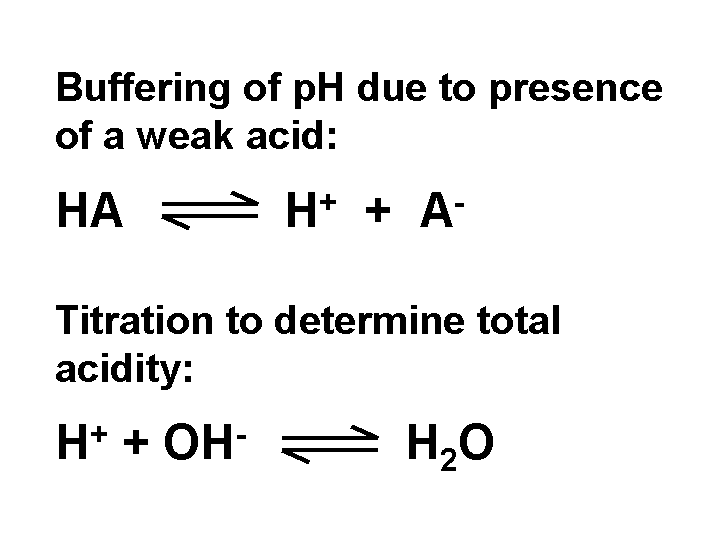
Adsorption
Adsorption means attachment to the outside of something. In the case of aqueous solutions one can consider adsorption of molecules, ions, and colloidal particles onto the surfaces of fibers, fiber fines, and fillers. Except for the special case of chemi-sorption, one does not have to assume that any chemical reaction takes place. Rather, the adsorbate (the thing that is adsorbed) is attracted to the surface by the net effects of electrostatics, London dispersion, and solvent structure (or entropy).
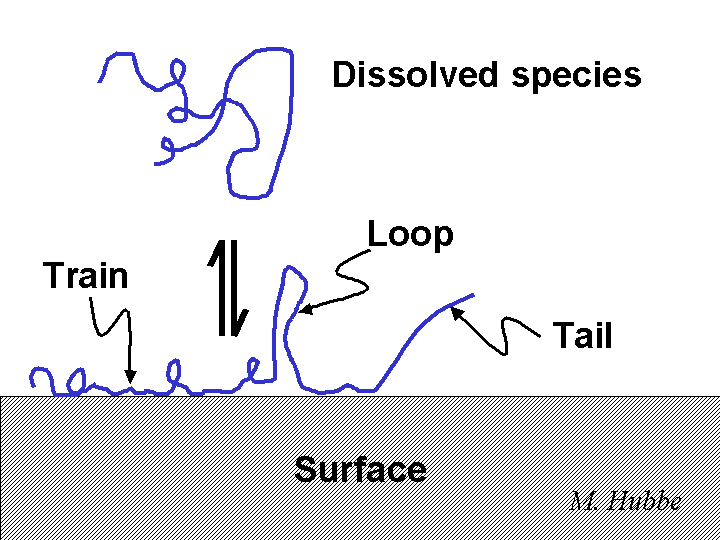
Alkalinity
The alkalinity of an aqueous system equals the amount of strong acid (such as HCl) consumed when the pH of a unit volume is titrated to a methyl-orange endpoint (pH approx. 4.0). Relatively high levels of alkalinity may be due to the presence of bicarbonate ions, carbonate ions, calcium carbonate filler. Alkalinity tends to consume papermaker’s alum (Al2(SO4)3.14H20).
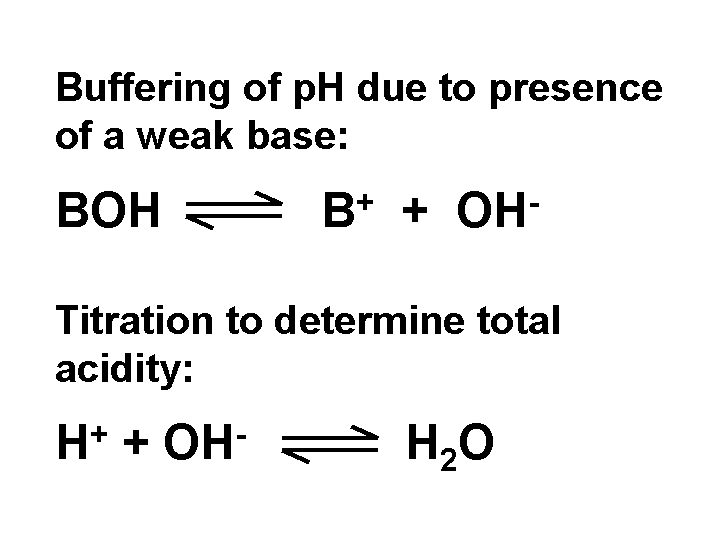
Anionic
A substance is considered anionic if it has a net negative charge. For example, the chloride ion Cl- is anionic. Many polyelectrolytes are also anionic. Sodium polyacrylate is a one example. When this polymer is dissolved in water, the sodium ions are partly dissociated from the polymer chain. Many types of particles of interest to papermakers tend to have an anionic surface charge when suspended in water solution. Though there are an equal number of positive and negative ions in the sample as a whole, the net negative surface of an anionic particle is balanced by counter-ions in solution. The words “double-layer” are used to describe the distribution of counter-ions adjacent to a charged surface.
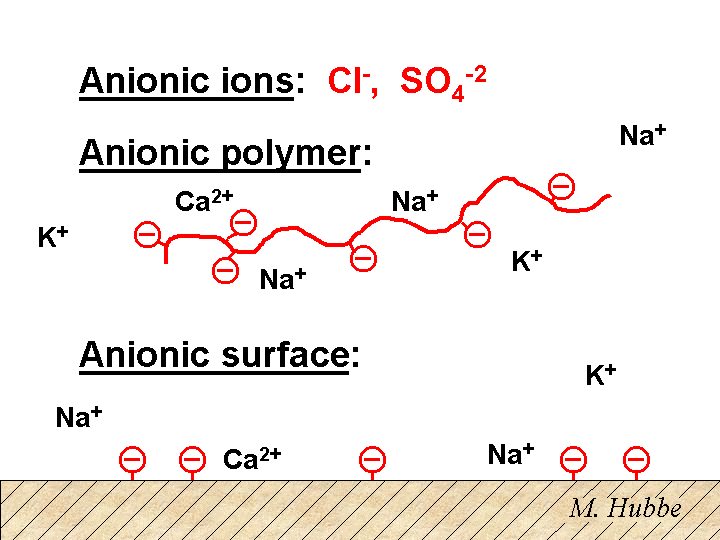
Ash
Papermakers use the word “ash” in two ways. In its most general sense, the word means “filler” or “mineral content.” The word also refers to the material that is left over when paper is incinerated at a defined temperature and for a defined time. A relatively high temperature of incineration, such as 900 degrees Centigrade, can drastically change the chemical composition of the filler. For instance calcium carbonate is converted to CaO, which has a mass only 56% that of the filler. Kaolin clay looses water under such conditions; the anhydrous clay has 86% the mass of the hydrous filler clay. A moderately low temperature of incineration, e.g. 500 degrees Centigrade, may leave most of the filler in its original form. To convert “percent ash” data to “percent filler” it is necessary to know the relative amounts of the different fillers and their respective losses on ignition. The relative amounts of, say clay versus calcium carbonate, can be determined by x-ray fluorescence analysis of the incinerated ash.
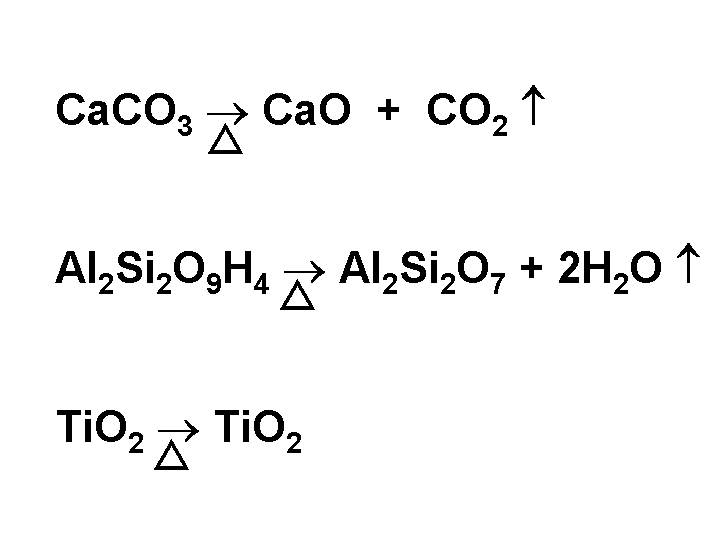
Bridging
Bridging is a term used to describe the ability of certain dissolved polymers to agglomerate suspended particles or to cause flocculation of fiber slurries, especially in the presence of flow. According to the bridging model, the polymer first adsorbs partly onto one surface, and then loops or tails or the same macromolecule become attached to a second surface. Dissolved polymers need to have a molecular mass of at least 2 million grams per mole in order to work effectively by this mechanism. An anionic polyelectrolyte can be a very effective bridging agent and retention aid for papermaking fibers if these have been treated with a cationic material so that there are positive sites on those surfaces.
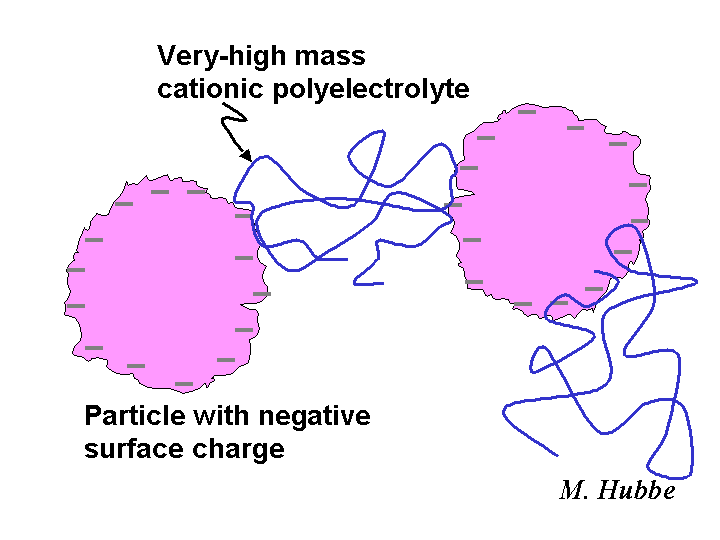
Cationic
A cationic material has a net positive charge. Positive ions such as the sodium ion are cationic. A polyelectrolyte is called cationic if its chain has a positive charge after dissociation of monomeric counter-ions such as chloride or acetate. Likewise, a suspended particle is cationic if it has a net positive charge at its surface. A cationic particle is always surrounded by a cloud of excess counter-ions so that the total number of charges add up to zero.
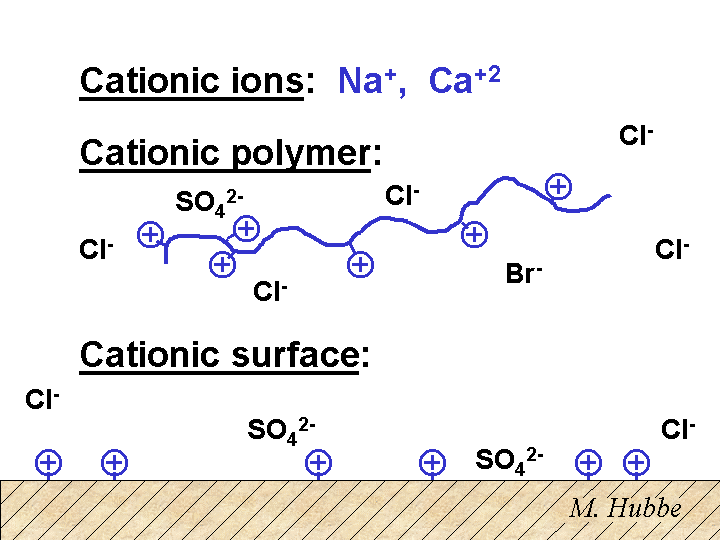
Cationic Demand
The cationic demand of a sample of paper making furnish or process water equals the amount of highly charged cationic polymer required to neutralize its surface. The most common titratant for such tests is poly-DADMAC. The streaming current test is often used to determine cationic demand, based on the amount of cationic titrant required to reach a zero signal. Another way to determine the endpoint is by evaluating the zeta potential after each incremental addition of titrant. Data related to zeta potential can be evaluated by microelectrophoresis or streaming potential methods. Because polyelectrolytes can penetrate into the pore structure of fiber cell walls, the results of such experiments depend on the molecular weight of the titrant. Also it is necessary to use a reproducible, steady rate of titration in order to get reproducible results. Another strategy for determining cationic demand is to mix the sample with a known excess of cationic titrant, filter to remove the solids, and then back-titrate to a color endpoint (colloidal titration). It is a widely recommended strategy to maintain cationic demand of a papermaking furnish at a constant, but usually non-zero level.
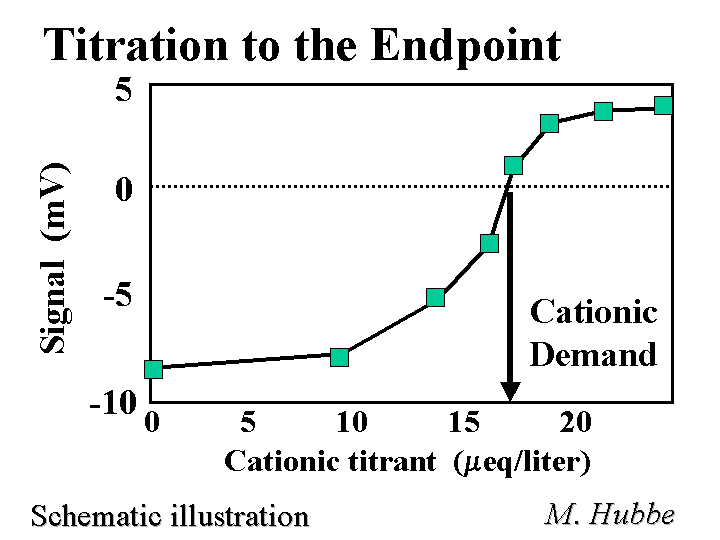
Charge
The word “charge” can be used in two ways. In its broader sense, the word refers to the sign of the net electrical potential at the surface. For example, it is accurate to say that a clay particle has a negative charge. In its narrower sense the word “charge” refers to colloidal charge demand, the number of net charge equivalents that can be consumed per unit volume or mass of sample (e.g. 4.3 microequivalents per liter). A titration procedure is required to determine the charge demand of a process sample. The total surface charge of a papermaking fibers suspended in distilled water can be determined by titration with acid or base, starting at a pH value near to 2.5, where zeta potential equals zero. The external charge demand (which is sometimes taken as an estimate of external surface charge) of papermaking materials from a paper mill process stream can be estimated by titration with a polyelectrolyte – realizing that molecular mass determines which of the pores are accessible during the titration.
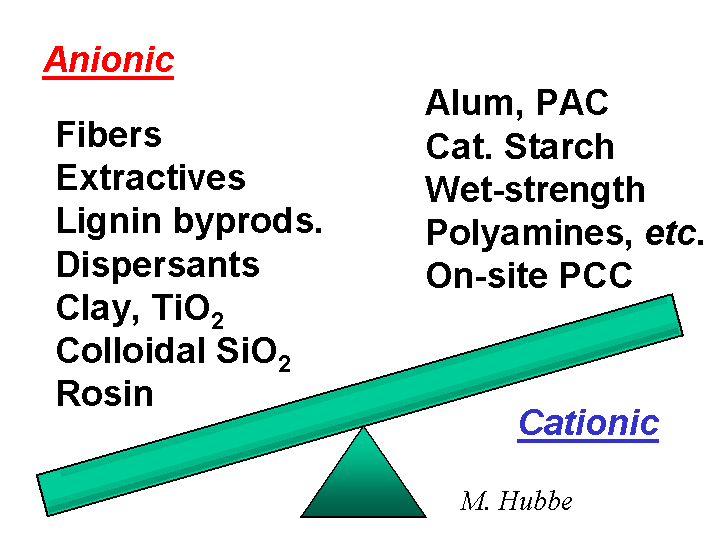
Charge Neutralization
Charge neutralization refers to a state in which the net electrical charge of particles, fibers, colloidal material and polyelectrolytes in aqueous solution have been canceled by the adsorption of an equal number of opposite charges. Usually these opposite charges are supplied by a multi-valent material. For example alum, with its tri-valent cations, is effective for neutralizing the negative charge of rosin soap at acidic pH. Quaternary polyamines and other highly charged cationic polymers are very effective for neutralizing the charge of anionic particles over a very wide range of pH. A state of charge neutralization is often associated with the most rapid coagulation of suspensions and the most rapid drainage of papermaking furnishes.
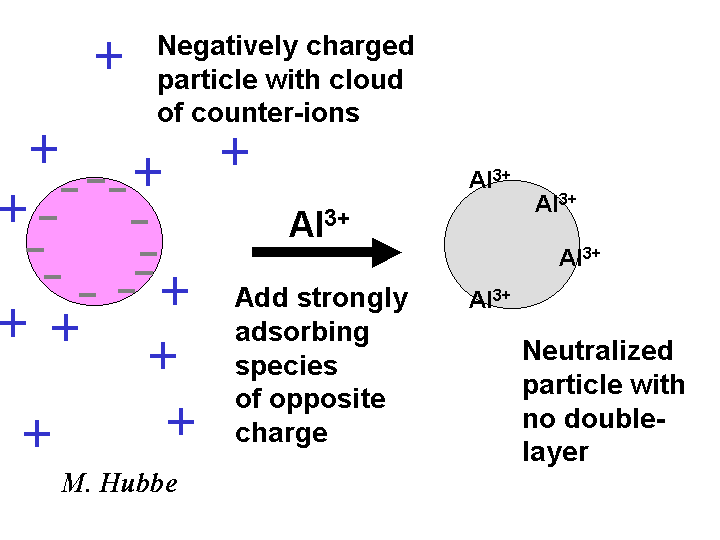
Charged Patch Model
The charged patch model is one of the descriptions that scientists use to account for the main effects of highly charged cationic polyelectrolytes having molecular masses in the approximate range of 100,000 to 2 million grams per mole. The patch model appears especially appropriate in cases involving polyelectrolytes having a branched structure adsorbing onto surfaces of opposite charge. The adsorbed patch of polymer can serve as an anchoring point for another bare surface of the same type as the first. The strongest evidence in favor of a charged-patch mechanism is the partial reversibility of certain flocculation, retention, and drainage phenomena. In other words, particles that have been detached from each other by strong hydrodynamic forces can be effectively linked together again by the charged patches. By contrast, polymeric bridges between suspended particles tend to be irreversibly broken by high levels of shear.
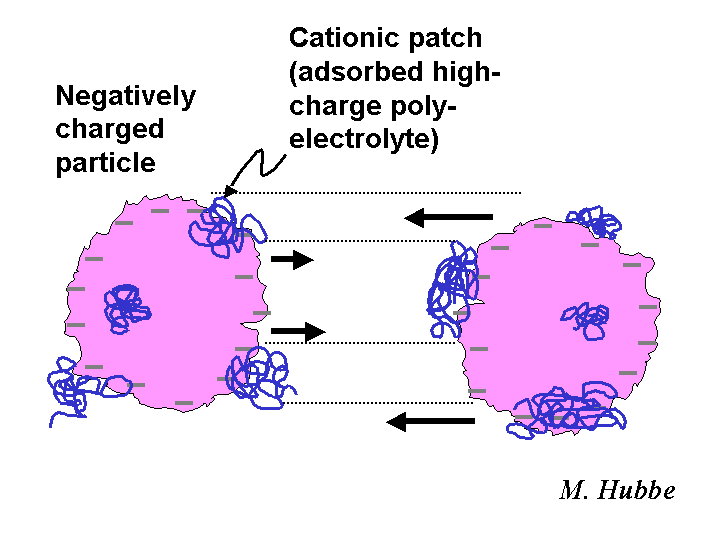
Coagulation
The word coagulation means that fine particles in a suspension collide with each other and stick together. Usually the particles are brought near to each other by Brownian motion or by flow. Brownian motion is a random migration of particles due to collisions with solvent molecules. The rate of Brownian motion can be predicted from the temperature, the size of the particles, and the viscosity of the solution. Flow effects tend to overwhelm Brownian migration rates in the case of particles larger than 1 micro-meter. Factors which tend to make fine particles stick together after a collision include (a) lack of strong electrostatic or steric repulsive forces, (b) London dispersion forces, a type of Van der Waals force, and (c) polyelectrolyte bridges or patches. The presence of water-loving hemicellulose and cellulose macromolecules extending from papermaking fibers tends to weaken coagulation effects in papermaking suspensions.
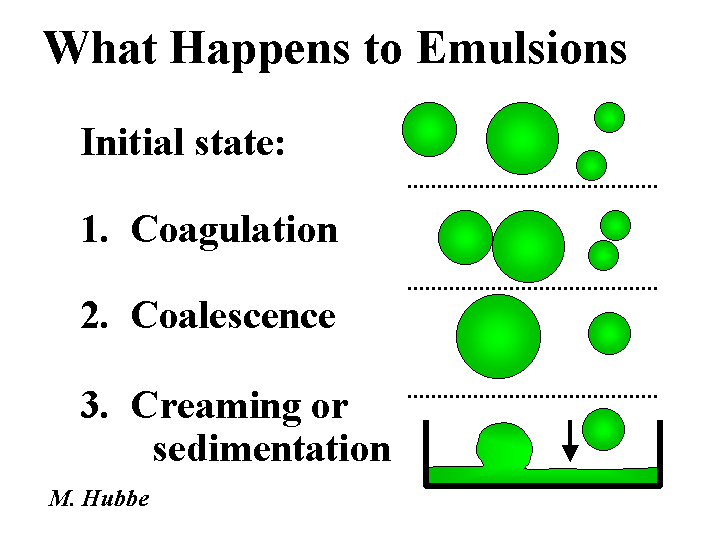
Colloid
A colloidal substance has the following attributes: (a) at least two phases, (b) at least one dimension of a liquid or solid phase than is less than one micro-meter, and (c) properties that are dominated by interactions within and between surfaces. Examples of colloids are suspensions, emulsions, foams, and aerosols. Most colloids are thermodynamically unstable. Given enough time, most foam bubbles pop, and most suspensions coagulate or settle. Many colloids can be stabilized by additives that decrease the interfacial tension, i.e. the free energy per unit area of surface. Such substances are known as surface-active agents or surfactants. Aqueous suspensions and emulsions can be further stabilized by addition of suitable water-loving polyelectrolytes to the aqueous phase (see steric stabilization).
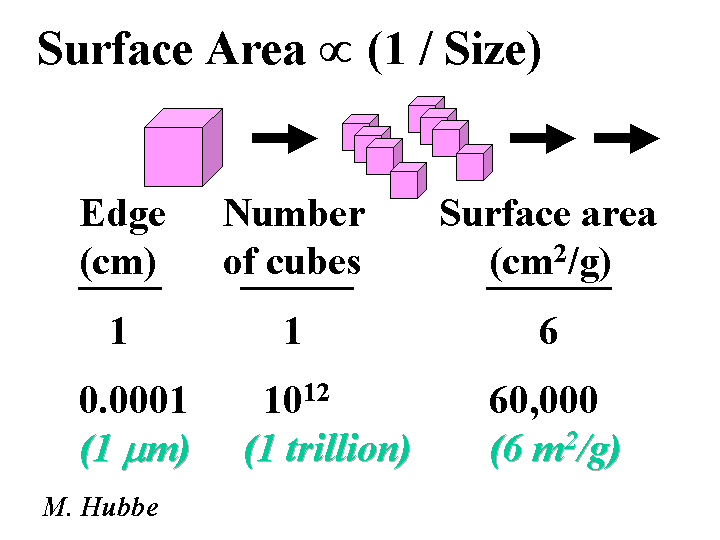
Colloid Titration
The colloid titration method is one way to estimate the net charge density of surfaces, polyelectrolytes, and the charge demand of colloidal materials in an aqueous mixture. What is actually measured is the capacity of the mixture to adsorb a polyelectrolyte of opposite net charge. In a typical case the mixture is first treated with a known excess of highly cationic polymer such as poly-DADMAC. Then it is filtered or centrifuged to remove solids. A small amount of indicator dye (usually toluidine blue-O) is added to a known volume or filtrate or supernatant solution. The blue solution is back-titrated with an anionic polyelectrolyte such as potassium polyvinylsulfate (PVSK) to a purple-pink endpoint. Complexation between the dye and the negatively charged polymer causes the color-change. Though the method can be a quick and reliable way to estimate charge demand of process water samples and fibrous slurries from paper mills, the results tend to be off-set from related methods based on electrokinetic measurements.
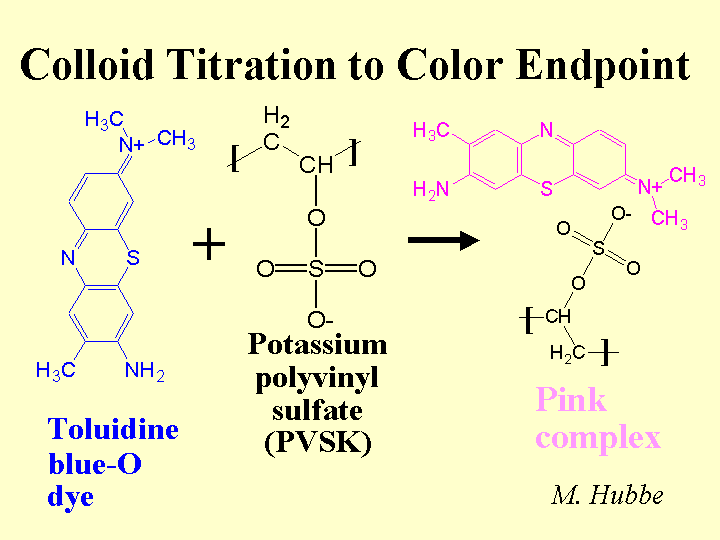
Consistency
When papermakers use the word “consistency” they usually mean the same thing as “solids” or “percent solids.” Consistency is usually measured by collecting the slurry solids on a tared filter paper, drying the paper at 105 degrees Centigrade, and dividing the mass of the solids by the mass of the original slurry. Consistency also can be estimated by light scattering and depolarization measurements at one or more wavelengths; however, it is recommended that optical data be frequently recalibrated with representative samples of furnish or white water from the system of interest.
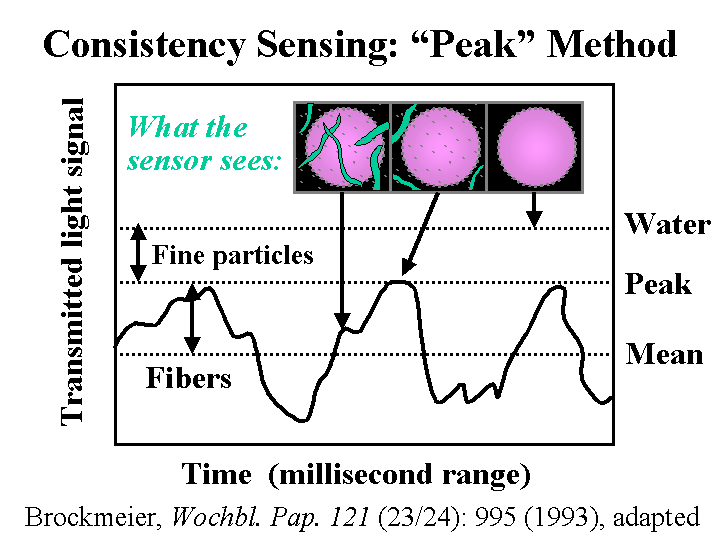
Critical Surface Tension
The critical surface tension of a solid surface is an indication of its relative water-hating or water-loving character. A low critical surface tension means that the surface has a low energy per unit area. The quantity is based on experiments with a series of pure liquids. These experiments have to be conducted on a flat, non-porous sample of that solid. A small droplet of each liquid is placed onto the surface. One measures the angle of contact at the solid-liquid-air contact line. The angle is drawn through the liquid phase. One plots the cosine of the angles of contact versus the surface tension of each liquid. For example, the surface tension of water, in equilibrium with its vapor at room temperature, is 72 mNm-1. Surface tensions of other liquids are widely available. The critical surface tension equals the surface tension at which the plotted line intersects 1.0.
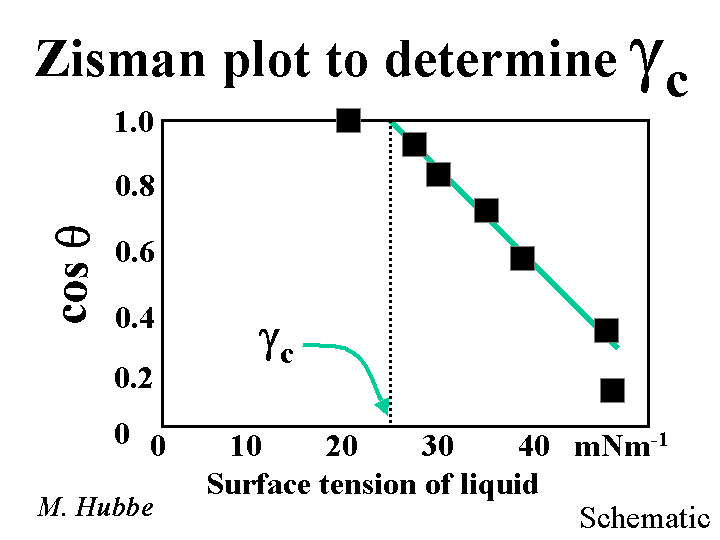
Crowding Factor
The crowding factor of a fibrous slurry is a way to predict the relative degree to which it will become flocculated by the action of hydrodynamic shear forces alone, even in the absence of attractive forces between the solids. The theory behind the factor is related to the amount of “room” a fiber needs to rotate without touching other fibers. The crowding factor is directly proportional to the consistency. It is proportional to the square of the ratio of fiber length to diameter. Two furnish samples having the same crowding factor are likely to yield sheets having the same uniformity of formation, assuming that all other factors are equal.
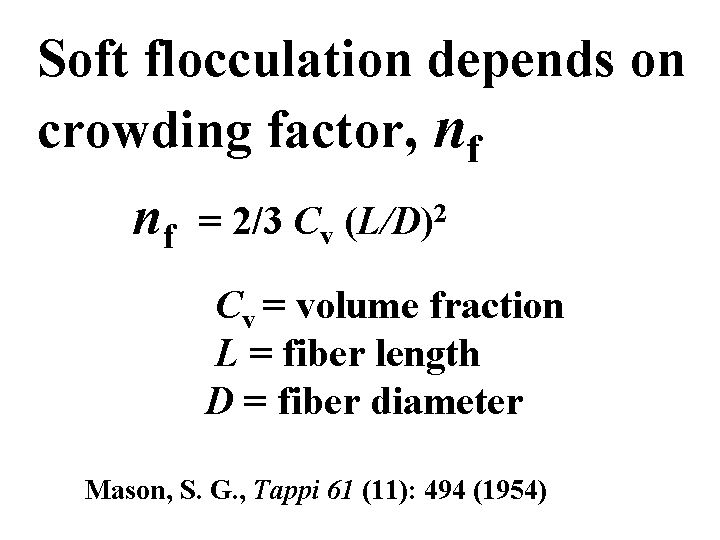
Dispersion
The word “dispersion” has at least three distinct meanings that are relevant to papermaking chemistry. A colloidal dispersion is a suspension of very small solid particles, as in the case of a filler slurry. By contrast, we call it an emulsion of the suspended entities are liquid, or at least if they were liquid when the emulsion was formed. “Dispersion” is also the act of dispersing materials to make a suspension. Finally, the most universal component of attractive forces between colloidal particles is known as the London dispersion component of attractive force. Such forces arise due to the momentary dipoles created by movements of electrons in orbitals surrounding the adjacent atoms on different small objects. (The reason that an attractive force got this illogical name has nothing to do with the act of dispersing colloidal dispersions; rather, it is because the forces are related in theory to the dispersion of light by a prism.)
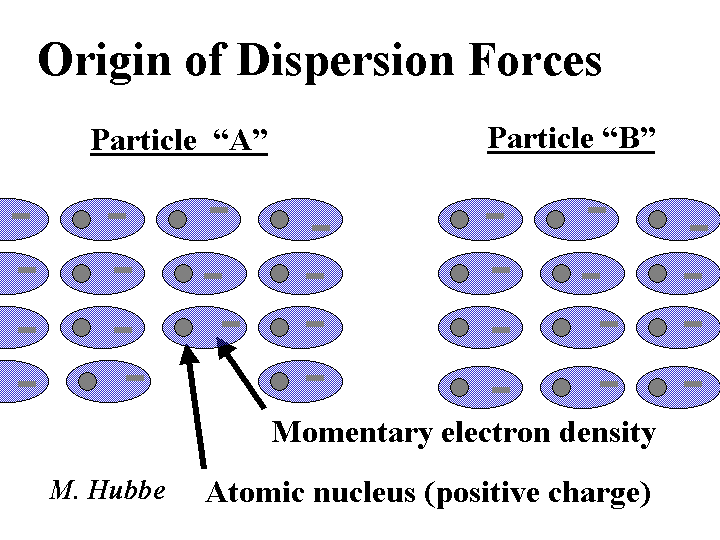
Double Layer
The words “double layer” refer to displacement of electrical charges associated with most surfaces exposed to aqueous solution. The layer is “double” because it involves two parts – the net charge on the surface, and the cloud of excess counter-ions in the adjacent solution. There have been many studies aimed at understanding how ions are distributed within the counter-ion field. Most colloidal phenomena are described quite well by a model in which the counter-ions are distributed between two regions. In the Stern layer (condensed layer) the ions are pressed against the surface. Out beyond the Stern layer the ions are distributed in a diffuse atmosphere, the Gouy layer. The density of ions within this layer is given by the Poisson-Boltzmann relationship. At distances of much more than 10 nm from surfaces (under typical electrolyte conditions) there is an equal density of positive and negative ions.
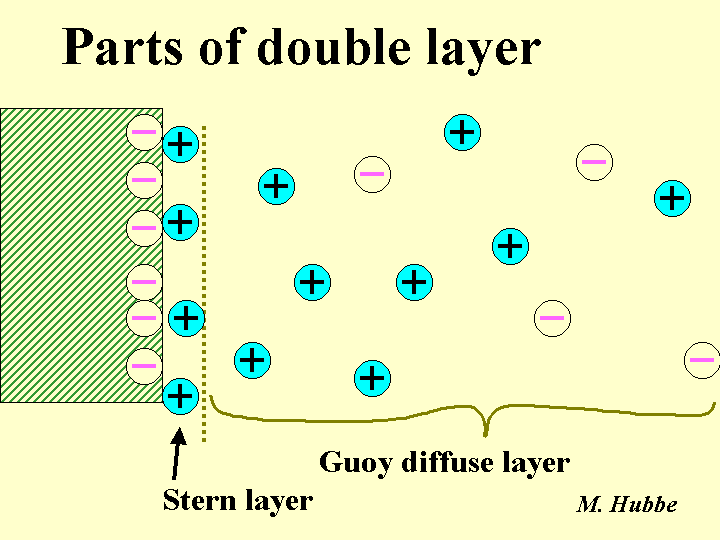
Drainage
The word “drainage” refers to the ease with which water is released from papermaking furnish, especially in the early part of a paper machine’s forming section. The word “dewatering” is more general, including the effects of vacuum and pressing as means of getting water out of the wet web. Drainage tends to be inhibited by the presence of fiber fines, high basis weight webs, high levels of refining, and any excess of polyelectrolytes remaining in the solution phase. Drainage rates often can be increased by the use of highly cationic chemicals such as alum, polyamines, or PEI products. Microparticle programs are designed to increase drainage rates. Factors that increase fiber flocculation are likely to increase initial drainage rates, but they are also likely to hurt the performance of vacuum dewatering and pressing.
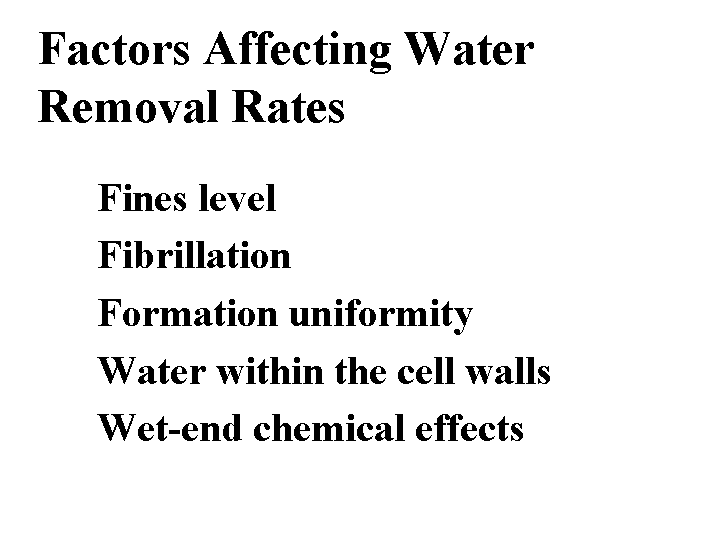
Dry Line
The dry line is the location on a Fourdrinier paper machine forming section where the appearance of the wet web of paper changes abruptly. Before the dry line the furnish has a glossy, wet appearance. After the dry line the wet web appears dull. The optical change is related to the effect of fibers poking through the air-water interface. On a well-adjusted paper machine the dry line ought to be straight. Increased refining and lower freeness of the pulp tend to move the dry line in the direction of the couch. Chemicals that promote drainage tend to move the dry line in the direction of the slice.
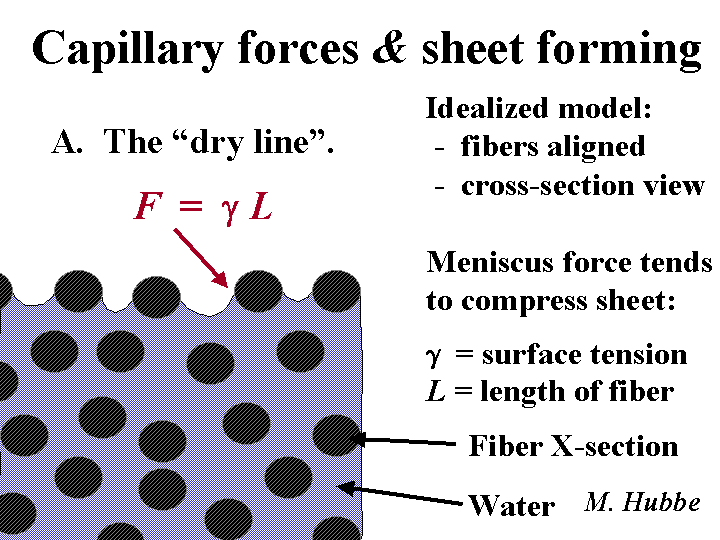
Dry Strength
Dry strength is a general term that applies to various destructive tests of paper. The word “dry” usually implies that the paper is in equilibrium with the 50% relative humidity condition of a standard testing laboratory. The words “dry strength” are most often associated with tensile strength, burst strength, and internal bond strength. Dry stength usually is increased by refining and by addition of starch products, etc. However, as shown below, tear strength may decline at some point if the increased bonding within a paper sheet has the effect of making it more brittle.
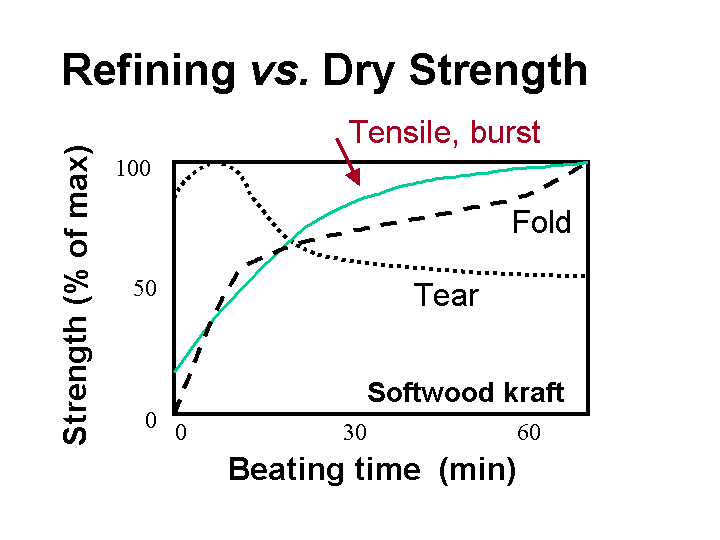
Emulsion
An emulsion is a colloidal dispersion of droplets of one liquid within another liquid. Milk is a familiar example of an oil-in-water emulsion. Rosin size emulsions are also of the oil-in-water type. We call rosin emulsions “emulsions” even though the droplets become solid when the mixture is cooled. Retention aids are commonly delivered to paper mills in the form of water-in-oil emulsions. This form of delivery makes it possible to ship retention aid at between 25 and 50% actives. The same polyelectrolytes would have to be diluted to about 2% solids in order to ship them as highly viscous solutions. Emulsions are thermodynamically unstable and the droplets tend to coalesce over sufficiently long periods of time. The stability of emulsions can be greatly increased by the use of suitable surface-active agents to decrease the free energy content of the interfacial area. Highly stable emulsions require the use of steric stabilizers, i.e., polyelectrolytes that cover all the surfaces with loops and tails extending into solution.

Extensional Viscosity
Extensional viscosity is of concern to papermakers because it can explain certain instances of slow drainage. The most familiar type of viscosity is shear viscosity, and it can be measured in a number of ways that involve the relative flow of a liquid and a solid object or wall. Likewise, extensional viscosity of a fluid can be evaluated by experiments in which the liquid converges or diverges. Such experiments have shown that solutions of polyelectrolytes tend to have very high levels of extensional viscosity. Makers of wet-laid nonwoven fabrics take advantage of this effect to achieve good formation of mats composed of long, slender fibers. Papermakers try to avoid having any residual polyelectrolyte in the solution phase, since usually they cannot afford the loss in drainage rate.
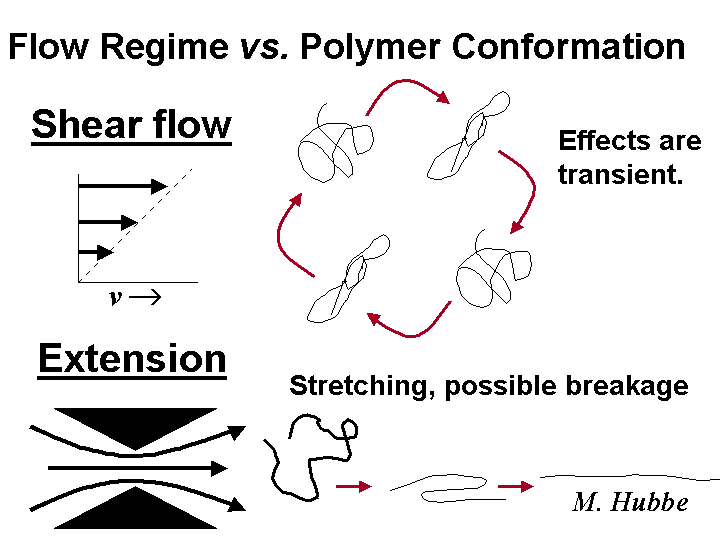
Fibrillation
The word “fibrillation” refers to both a process and the result of that process. Refining can be defined as the passage of a slurry of papermaking fibers between plates in relative motion to each other that have raised bars on their surfaces. The fibers are subjected to shearing and compression forces. One of the things that happens during refining of fibers is fibrillation, the partial delamination of the cell wall, resulting in a microscopically hairy appearance of the wetted fiber surfaces. The “hairs” are also called fibrillation. The smallest microfibrils may be as small as individual cellulose chains. Fibrillation tends to increase the relative bonded area between fibers after the paper has been dried.
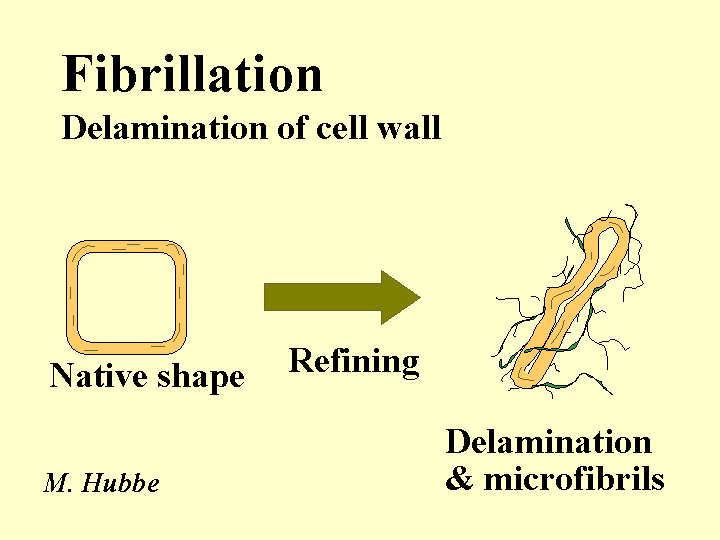
Fines (cellulosic)
The word “fines” most often means small cellulosic materials that are small enough to pass through a forming fabric. A TAPPI Useful Method defines fines as objects small enough to pass through a conical hole having a minimum diameter of 76 micro-meters. Fiber fines have two main origins. So-called “primary fines” consist of parenchyma cells and other small cells that exist within the wood. Kraft pulping releases them as intact, rod-like objects. By contrast “secondary fines” are produced by refining. A typical secondary fine tends to be ribbon-like. Secondary fines tend to favor strong inter-fiber bonds. Both types of fines tend to hurt drainage. It is worth keeping in mind that none of the preceding definitions deals with recycling of paper. It has been suggested that secondary fines, after they have been recycled, act more like primary fines in terms of their effectiveness at increasing paper strength. Some papermakers also include filler particles and other suspended material in the category of “fines.”
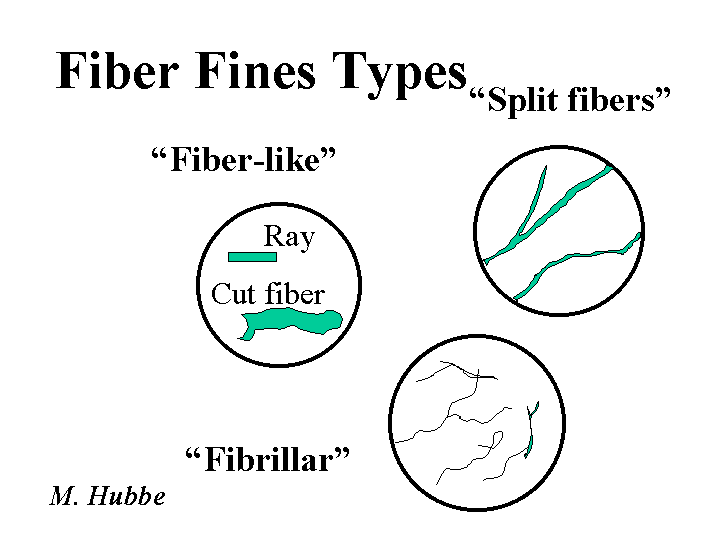
First-Pass Retention
First-pass retention gives a practical indication of the efficiency by which fine materials are retained in a web of paper as it is being formed. First-pass retention values can be calculated from just two consistency measurements, the headbox consistency, and the white water consistency. There is a very wide diversity of first-pass retention on different paper machines, from less than 50% to almost 100%. The key rules that papermakers follow are that (a) first-pass retention should have a steady value, and (b) that value should be high enough to avoid operational problems or an excessively two-sided sheet. Some operational problems that can be caused by low values of first-pass retention are increased frequency of deposit problems, filling of wet-press felts, poor drainage, and unsteady drainage rates and sheet moistures.
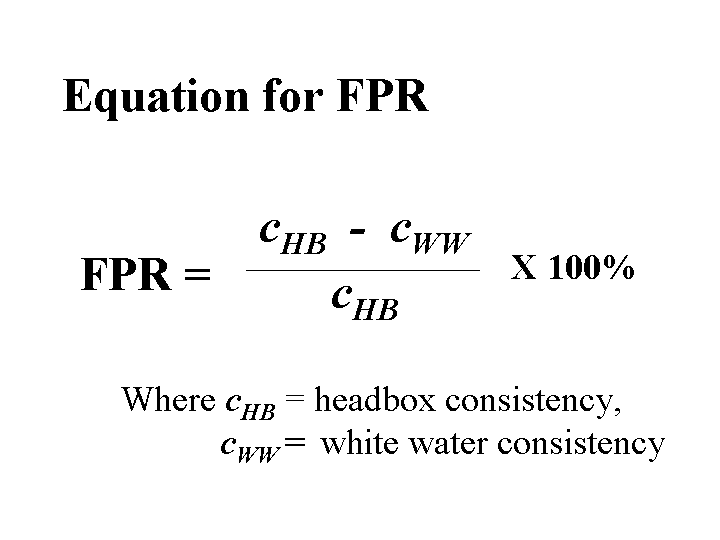
Flocs: Hard vs. Soft
When papermakers use the word “flocs,” they usually are referring to groups of fibers clumped together. Strong hydrodynamic forces, such as those present in fan pumps and pressure screens, can be very effective in redispersal of flocs. However, shear forces also cause fibers to bend. As the fibers straighten out, they may lock together again mechanically. Papermakers sometimes make the distinction between hard flocs and soft flocs. Hard flocs are those formed by very-high-mass retention aid polymers. Hard flocs a quite strong, but when broken, they are not able to form as strong flocs the next time. By contrast, soft flocs are readily broken by moderate levels of shear, and they are completely reversible. Factors causing soft flocs to form include colloidal forces of attraction and the previously mentioned effects of shear flow. It is worth keeping in mind that colloidal chemists and water-treatment specialists use the word “flocs” to denote voluminous or gel-like particles formed as a result of high-mass polyelectrolytes in the absence of fibers.
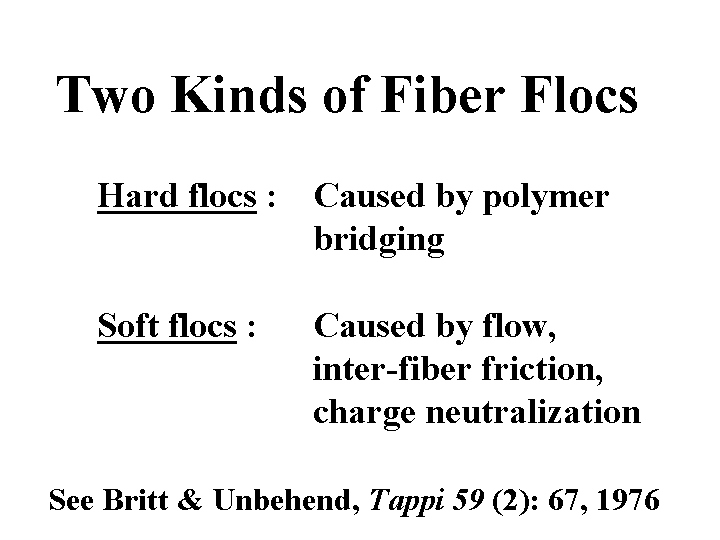
Formation
The word “formation” can mean either a paper characteristic or a process. As a paper characteristic, the word is usually a synonym for “relative uniformity over a scale of a few centimeters.” In the sense of process, the word is a synonym for “forming,” the assembly of fibers into a sheet as water is removed. The formation uniformity of a sheet of paper can be judged by viewing it with light from the back. The appearance of poor formation is usually related to fiber flocs persisting in the furnish through the process of form. Streakiness due to wake effects also contributes to poor formation.
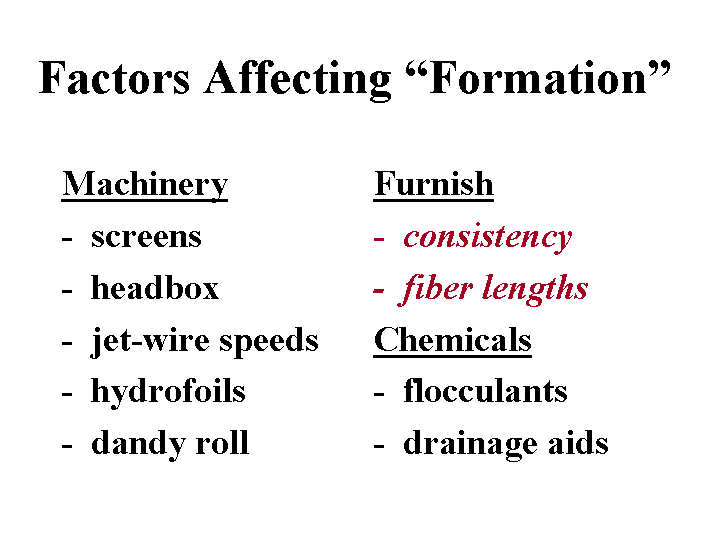
Freeness
Freeness is a measure of how quickly water is able to drain from a fiber furnish sample. In many cases there is a correlation between freeness values and either (a) a target level of refining of pulp, or (b) the ease of drainage of white water from the wet web, especially in the early sections of a Fourdrinier former. Standard tests of freeness are based on gravity dewatering through a screen. The devices are designed so that an operator can judge the speed of dewatering by observing the volume of liquid collected in a graduated cylinder. Freeness tends to be decreased by refining and by increases in the level of fines in the furnish. Freeness can be increased by use of drainage aids, removal of fines, or enzymatic treatments to convert mucilaginous materials into sugars.
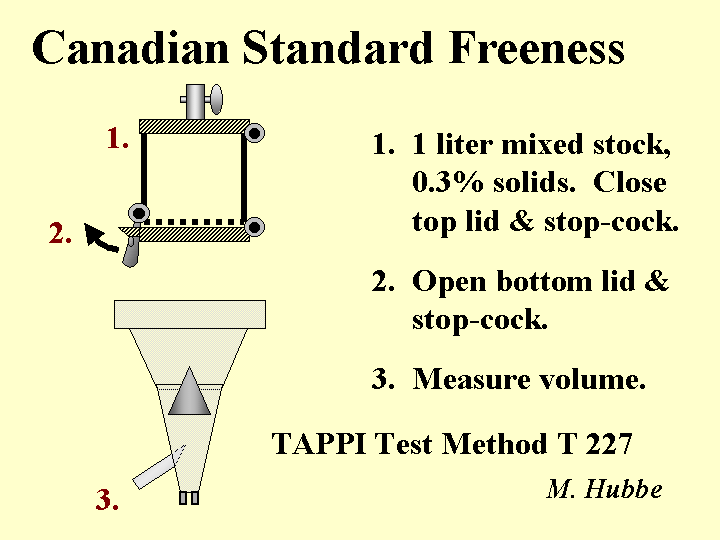
Hydrogen Bonding
Hydrogen bonding is one of the primary mechanisms by which papermaking fibers adhere to each other in the dry state. This is possible because cellulose and hemicellulose, two of the main components of papermaking fibers, are covered with hydroxyl groups. The oxygen atoms in these groups are able to hydrogen bond to hydrogen atoms on adjacent fibers or water molecules. Drying of paper causes some fiber-to-fiber hydrogen bonds to take the place of fiber-to-water hydrogen bonds. Recycling of paper is relatively easy because addition of water reverses this process. Hydrogen bonds have only about 5% of the energy content of a covalent bond.
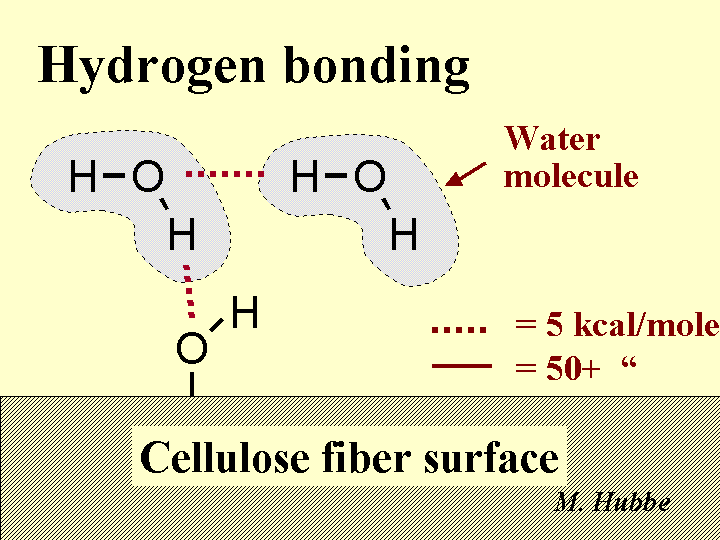
Hydrophilic
Hydrophilic means “water-loving.” Chemical groups that tend to make substances hydrophilic include ionic (charged) groups and groups that contain oxygen or nitrogen atoms. Starch is an example of a hydrophilic polymer. Cellulose fibers are hydrophilic due to the presence of -OH groups at their surfaces. The opposite of hydrophilic is hydrophobic, or water-hating. Surface-active agents contain both hydrophilic and hydrophobic groups on the same molecules.
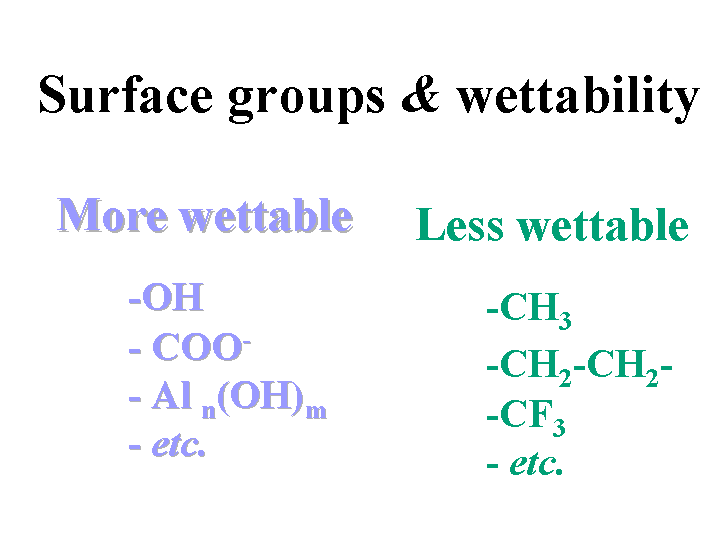
Hydrophobic
Hydrophobic means “water-hating.” Chemical groups that tend to make substances hydrophobic include -CH2- chains and rings (hydrocarbons). These substances lack the ability to hydrogen bond and their surface free energy is relatively low. Water does not tend to wet hydrophobic surfaces; rather, the droplets stay beaded up with high values of contact angle. Internal sizing agents such as rosin, ASA, and AKD depend on hydrophobic groups in order to perform their function. The opposite of hydrophobic is hydrophilic, water-loving. Surface-active agents contain both hydrophobic and hydrophilic groups on the same molecules.
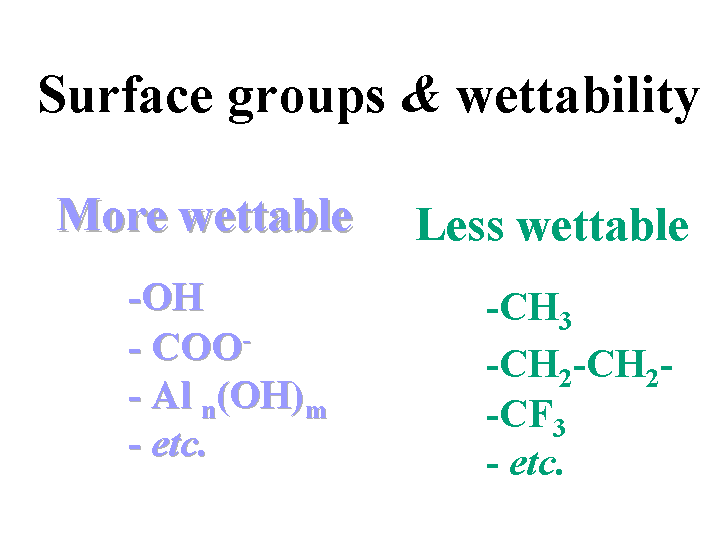
Interfering Substances
The term “interfering substances” is used by papermakers to explain poor performance of retention aids, sizing chemicals, and other additives in certain papermaking furnishes. Some of the best-known types of interfering substances consist of anionic dissolved polyelectrolytes and colloidal substances (DCS or anionic trash). These anionic substances can neutralize cationic additives and interfere with their function or their retention. Other substances that can interfere with papermaking operations include surfactants, salts (high conductivity), fines, and residual bleaching chemicals.
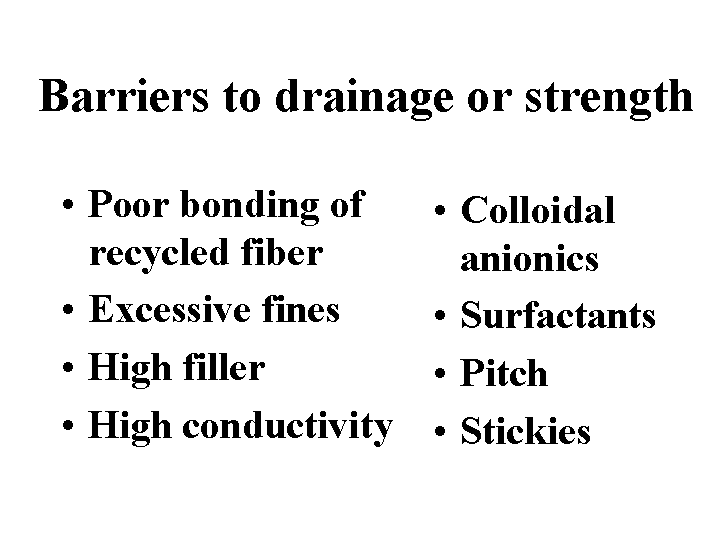
Jet-to-Wire Speed Difference
Papermakers adjust the jet-to-wire speed difference to fine-tune the paper structure. The “jet” is the narrow stream of papermaking furnish that comes out of the slice opening from the headbox. The “wire” is the continuous belt of forming fabric. Often it is possible to improve the uniformity of paper by running at a non-zero jet-to-wire speed difference. “Rushing the sheet” means that the jet speed is higher than the wire speed. “Dragging the sheet” means that the wire speed is higher than the jet speed. Especially in the case of dragging, increasing values of jet-to-wire speed difference tend to align fibers in the machine direction.
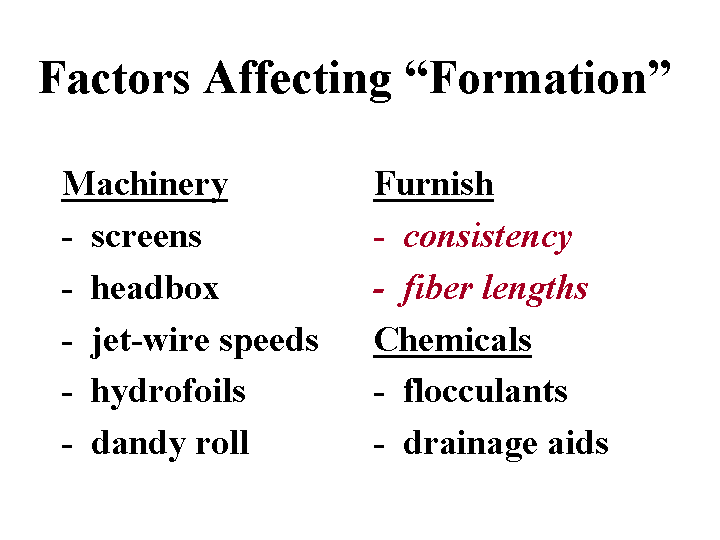
Metamerism
You know you have an instance of metamerism if two paper sheets look identical under one set of lighting conditions, but they appear to have a different shade from each other under a different illuminant. The major causes of metamerism problems are (a) poor selection of dyes when the same grade is made on different paper machines, (b) different effective levels of fluorescent whitening agents, especially in white grades, and (c) attempting to make the same grade with very different types of fiber furnish. Metamerism in color paper grades usually can be avoided by making sure that the red, yellow, and blue dyes each have a similar hue to the dye used when making the standard that was approved by the customer.
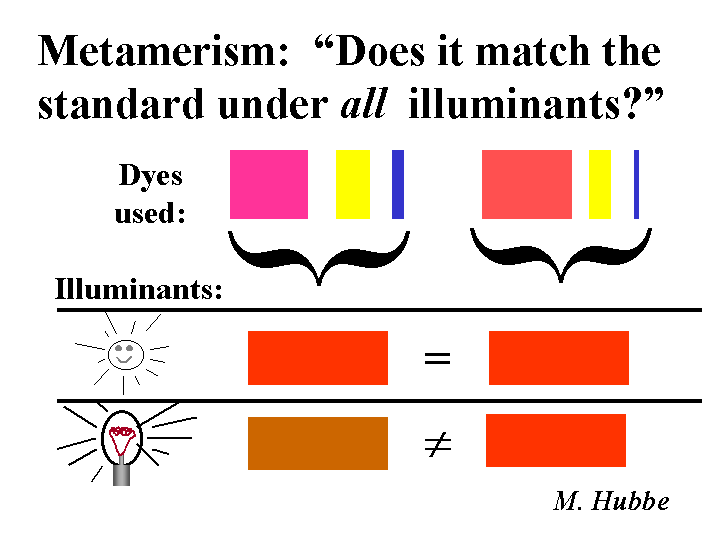
Microelectrophoresis
Microelectrophoresis is the best-known method for determination of zeta potentials of fiber fines and filler particles in paper machine white water. The apparatus includes a capillary cell, two chambers that include electrodes, and a means of observing the motion of particles. Because the capillary diameter is usually smaller than the length of a cellulosic fiber, these may be removed by filtration through a screen before the test. The apparatus is filled with very dilute suspension and the chambers are closed. A direct-current voltage is applied between electrodes in the respective chambers. One uses a microscope to determine the velocity of particles. The ratio or the velocity to the electrical field strength is known as the electrophoretic mobility. By making reasonable assumptions about the size of the observed particles and the electrical conductivity it is possible to calculate the value of the zeta potential. Zeta potential values near to zero indicate that the particles in the mixture are likely to stick together when they collide, unless they also are stabilized by non-electrical factors. Particles having a negative zeta potential are expected to interact strongly with cationic additives.
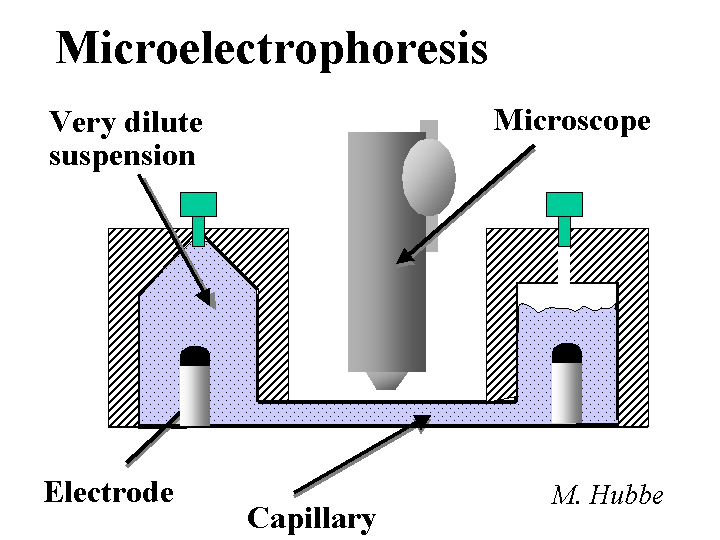
Microparticle Effect
The microparticle effect consists of a strong increase in drainage rates when a papermaking furnish is treated with anionic colloidal substances such as colloidal silica, bentonite, or certain highly branched anionic polymers. The effect is observed only if the furnish has been pretreated with (a) a sufficient level of cationic additives so that the furnish has a near-neutral or positive zeta potential, (b) a sufficient level of very-high-mass polymer such as cationic polyacrylamide or cationic starch, and (c) hydrodynamic shear to reduce the level of fiber-to-fiber flocculation.
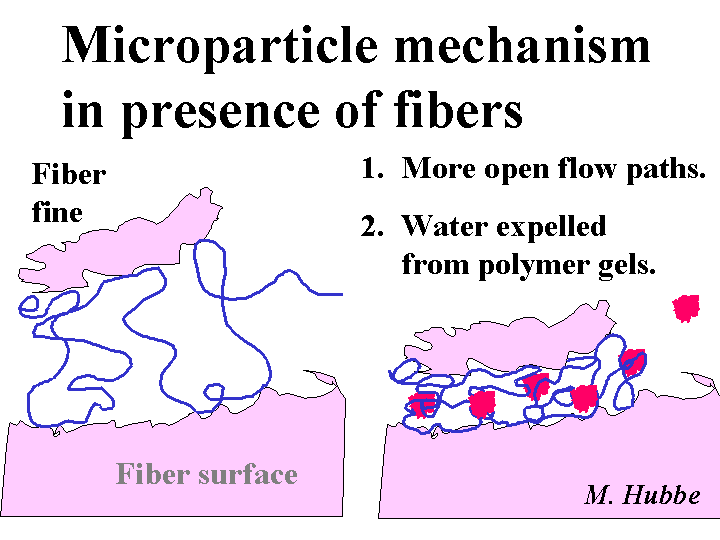
PATCH MECHANISM
The charged patch model is one of the descriptions that scientists use to account for the main effects of highly charged cationic polyelectrolytes having molecular masses in the approximate range of 100,000 to 2 million grams per mole. The patch model appears especially appropriate in cases involving polyelectrolytes having a branched structure adsorbing onto surfaces of opposite charge. The adsorbed patch of polymer can serve as an anchoring point for another bare surface of the same type as the first. The strongest evidence in favor of a charged-patch mechanism is the partial reversibility of certain flocculation, retention, and drainage phenomena. In other words, particles that have been detached from each other by strong hydrodynamic forces can be effectively linked together again by the charged patches. By contrast, polymeric bridges between suspended particles tend to be irreversibly broken by high levels of shear.
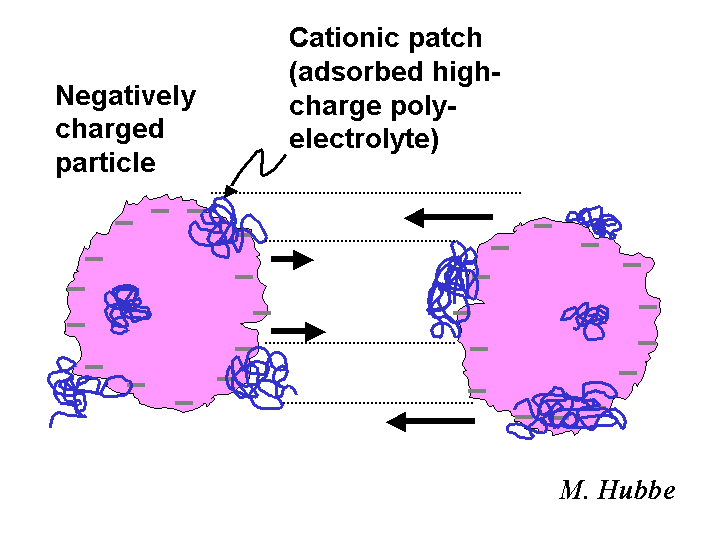
Plane of Shear
The plane of shear is a hypothetical location about 2 nm from the surface of a particle suspended in a typical sample of papermaking process water. Most phenomena related to surface charge and zeta potential can be explained by a model in which counter-ions closer to the particle that the plane of shear act as if they are attached to the particle. By contrast, ions outside of the plane of shear act as if they are part of the surrounding solution. The zeta potential is defined as the electrical potential at the plane of shear. Despite the fact that the location of the plane of shear usually is unknown, zeta potential values have been very useful for predicting whether suspensions are likely to coagulate.
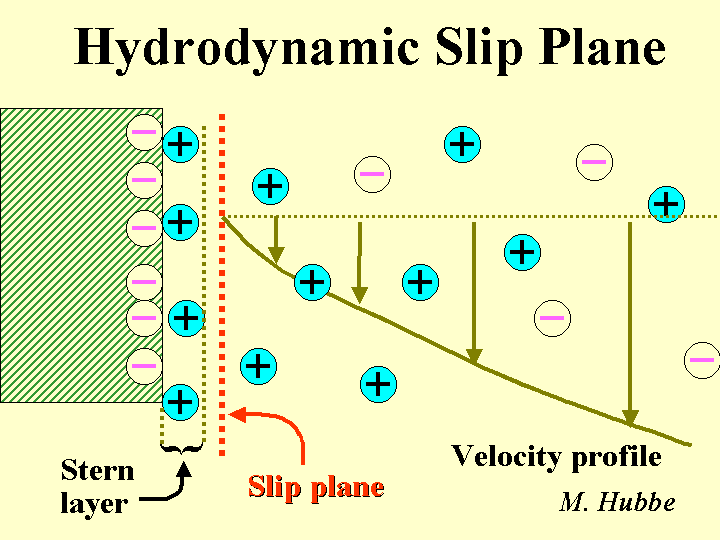
pH
The pH is the negative logarithm (base ten) of the hydrogen ion concentration in a solution. An increase of one pH unit implies a ten-fold increase in hydrogen ion concentration. At a neutral pH of 7 there are equal numbers of hydrogen ions and hydroxyl ions. The value of pH has a profound influence in papermaking because it affects the ionic character of fibers and many additives. Fibers tend to become increasingly anionic as the pH is increased in the range 3 to 8. Papermakers’ alum is strongly cationic under acidic papermaking conditions (3.5 < pH < 5.5), but it quickly loses its cationic charge after addition to alkaline furnish (7 < pH < 9). The acidity of a furnish equals the amount of strong base such as NaOH needed to raise the pH to 8.3.
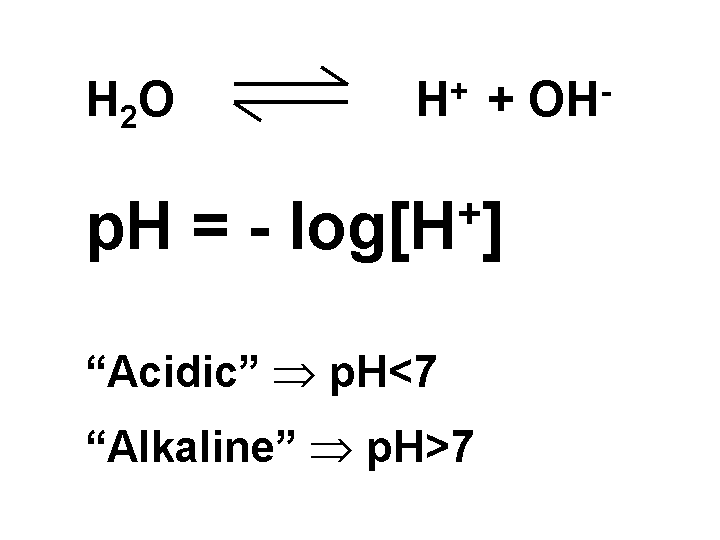
Polyelectrolytes
The word “polyelectrolytes” is a general term for water-soluble molecules comprised of many repeating units. As the name implies, most such materials of interest to papermakers have a significant level of electrical charge. In other words, small ions dissociate from the macromolecule, leaving a net charge associated with the chain. Many polyelectrolytes of interest to papermakers are linear, as in the case of cationic amylose starch. This compound makes up 28% of dent corn starch and 21% of potato starch. These starches are used to make cationic starch for wet-end addition. Many other polyelectrolytes are branched, as in the case of polyethyleneimine (PEI). Also, most starch products contain a majority of branched molecules called amylopectin. Cationic starch produced from waxy maize is about 100% branched molecules. Soluble aluminum products such as alum and PAC are often considered to be polymeric because of the formation of oxygen bridges between the aluminum ions (olation) during use.
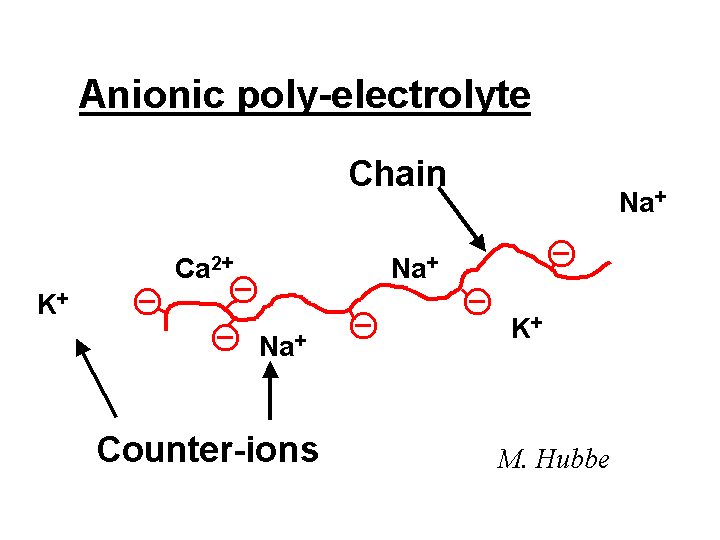
Relative Bonded Area
The relative bonded area between fibers is determined by light scattering. In theory the amount of light scattered by dry fibers is roughly proportional to their surface area. Part of that surface area effectively disappears in locations where fibers are very close together, i.e. in optical contact. The first step in determining relative bonded area is to form a paper sheet from the same fibers dispersed in a non-swelling solvent such as butanol. Such sheets have little hydrogen bonding between the fibers and very little strength. Light scattering does not give a true measure of bonded area because it is possible for parts of the fibers to be in optical contact (within about 200 nm) without being in molecular contact.
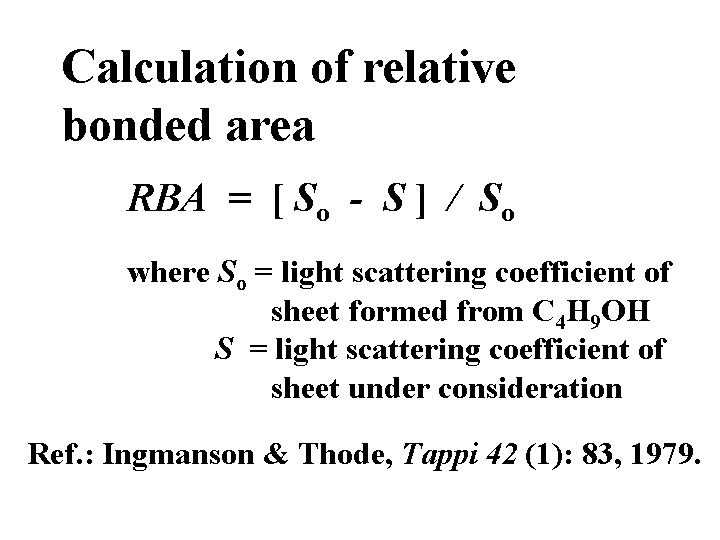
Retention
Retention is a general term for the process of keeping fine particles and fiber fines within the web of paper as it is being formed. The word also can be used to describe the efficiency of retaining small particles, as in “a high level of retention was achieved on this paper machine.” Retention can occur by various mechanisms. The simplest of these is mechanical sieving by the forming fabric. Once a fiber mat begins to form, the mat itself usually can act as a much more effective and finer sieve than the forming fabric. But even then, particles less than about 10 micrometers in size are not effectively retained by sieving. Rather, retention of fine particles requires the action of colloidal forces, including polymeric bridging or a charged patch mechanism. Retention aid chemicals can be effective either by attaching fine particles to fiber fines or fibers or by agglomerating them so that they can be sieved more effectively.
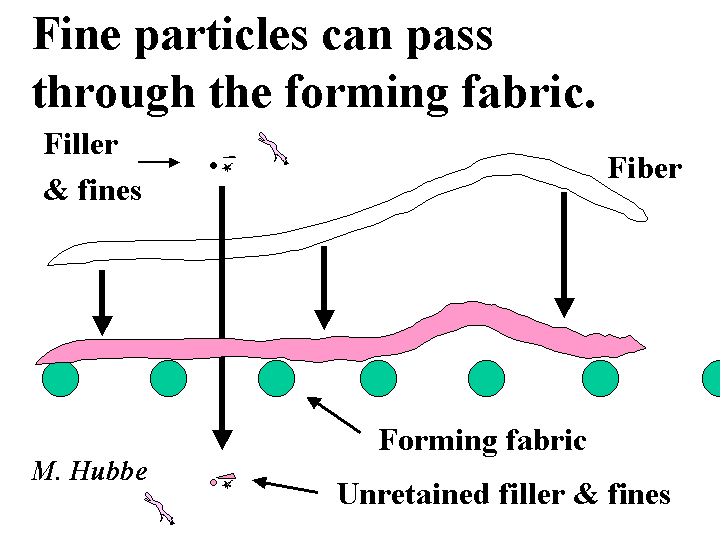
Reversibility of Flocculation
The term “reversibility of flocculation” refers to fibrous slurries that have been treated with a flocculating chemical and then dispersed by hydrodynamic shear. It has been observed that different chemical systems respond differently in this kind of situation. In general, very high molecular mass flocculants tend to behave irreversibly, meaning that the dispersed flocs do not form again to the same degree. By contrast, slurries that have been flocculated by highly charged polymers tend to behave reversibly. Not only to the fiber flocs form again, but also the levels of fines retention and drainage rates in jar tests tend to be independent of shear history. There is evidence that microparticle retention aid systems are partly reversible, and this might help explain how they perform on paper machines. In principle, the papermakers would like to have fibers remain well dispersed under conditions of shear in the approach system, but become attracted to each other for efficient retention aid drainage when on the forming fabric.
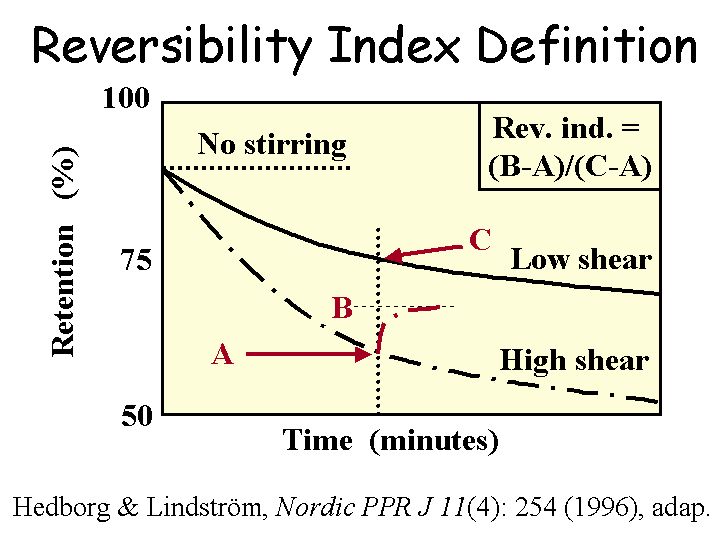
Site-Blocking
The site-blocking model has been used to account for the beneficial effect of certain pretreatment conditions on the action of flocculating chemicals and microparticle treatment programs. In principle there are two ways in which a highly charged cationic polymer can improve the flocculating ability of a very-high-mass cationic flocculant. On the one hand, it might help to neutralize excess anionic colloidal charges in the system that otherwise would have neutralized the charges on the flocculant. On the other hand, it can partly cover the surfaces, blocking many potential bonding sites. The high-mass cationic flocculant still may be able to find sufficient anionic sites on the furnish surfaces to become attached. However, the presence of the lower-mass cationic additive prevents the long chains from lying down. Instead, long loops and tails of polymer are expected to extend into the solution.
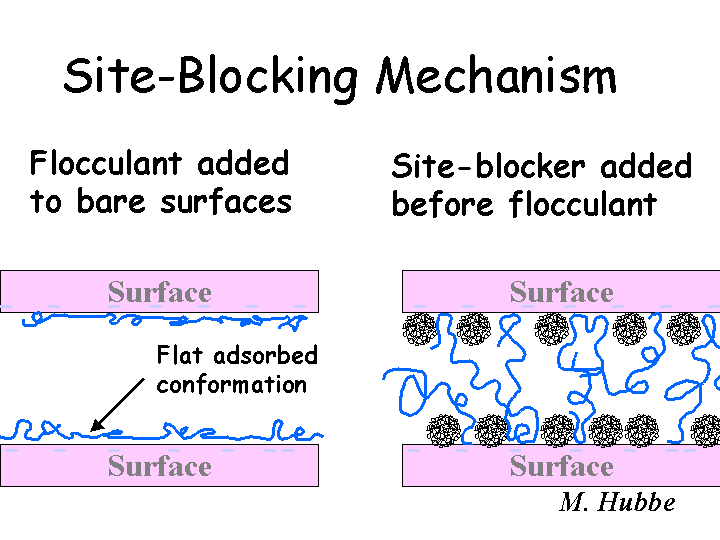
Stability
Papermakers and other technologists involved with slurries, emulsions, and dispersions use the word “stability” in a special way. A slurry, emulsion, or dispersion is said to be colloidally “stable” if it remains as individual particles. By contrast, an unstable mixture coagulates during the time of observation. Colloidal stability is highly desirable when one is considering the transportation and storage of rosin emulsions, TiO2 slurries, etc. However too high a level of colloidal stability in a papermaking system tends to make it difficult to retain fine particles during the formation of the sheet. High stability is favored by such factors as a high uniform zeta potential on the particle surfaces, the presence of surfactant (which may be charged), and the presence of water-loving polymeric loops and tails extending from the surfaces, i.e. steric stabilization. Destabilization of emulsions and dispersions can result from charge neutralization and by polymeric bridging.
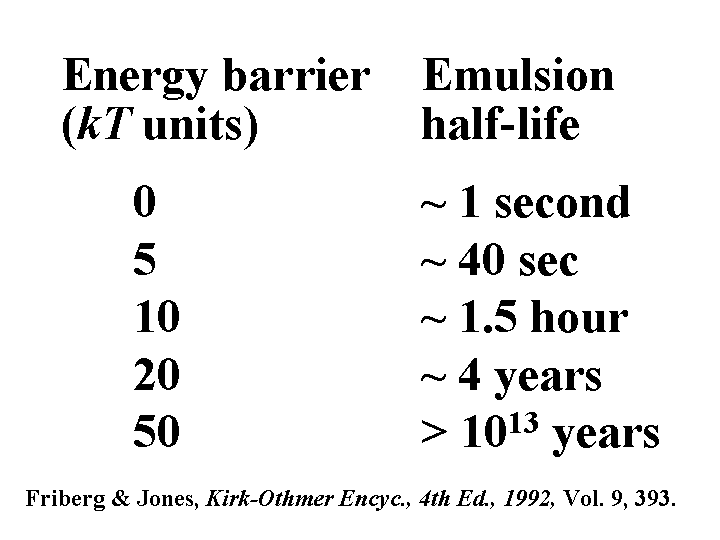
Stationary Level
The stationary level is a plane of focus within the capillary cell of a microelectrophoresis instrument. In the case of a cylindrical capillary this location is about 14.6% of the distance from one inner wall to the opposite inner wall. In the case of a rectangular cell the stationary level is located about 20% for the distance from one wall to the other. At the stationary level there is zero contribution to particle velocity from electro-osmosis. Instead, any observed particle motion can be attributed to either (a) electrophoretic mobility, or (b) Brownian motion. Electro-osmosis occurs because the capillary walls can have an electrical charge. When an electrical field is applied along the axis of the capillary it tends to pull some of the counter-ions adjacent to the wall. Associated fluid is moved along with the ions, creating a flow of solution. Because the chambers of a microelectrophoresis instrument are closed during use, a parabolic return flow occurs in the middle part of the capillary. Brownian motion can be defined as random movement of small particles in suspension due to chance collisions with adjacent molecules; Brownian motion is a consequence of thermal energy.
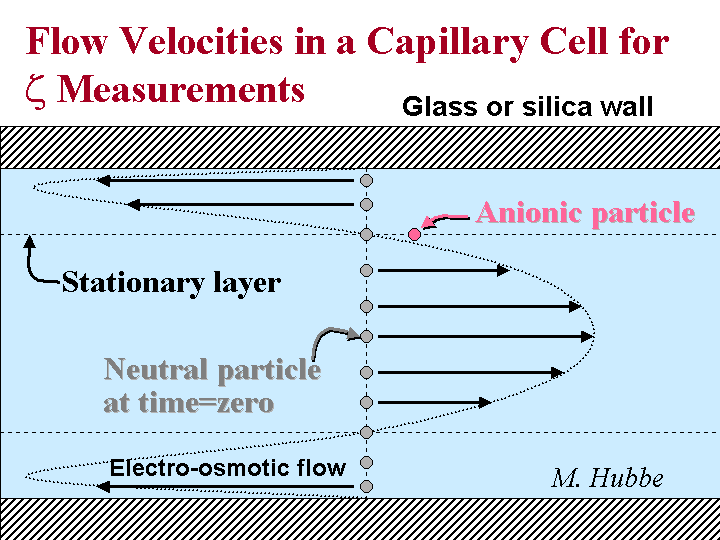
Steric Stabilization
Steric stabilization is a mechanism that can explain the ability of certain additives to inhibit coagulation of suspensions. These additives include certain water-loving polymers and surfactants with water-loving chains. These additives are believed to cover the system in such a way that long loops and tails extend out into solution. Systems that are sterically stabilized tend to remain well dispersed even at high salt concentrations or under conditions where the zeta potentials of the surfaces are reduced to near zero. The effectiveness of steric stabilizers has been attributed to the thermodynamic penalty when one tries to confine polymeric chains to smaller volumes. Another explanation is that such chains are water-loving, and they would rather stay associated with water, rather than interact with any other surface (except that they are attached at one end to a surface).
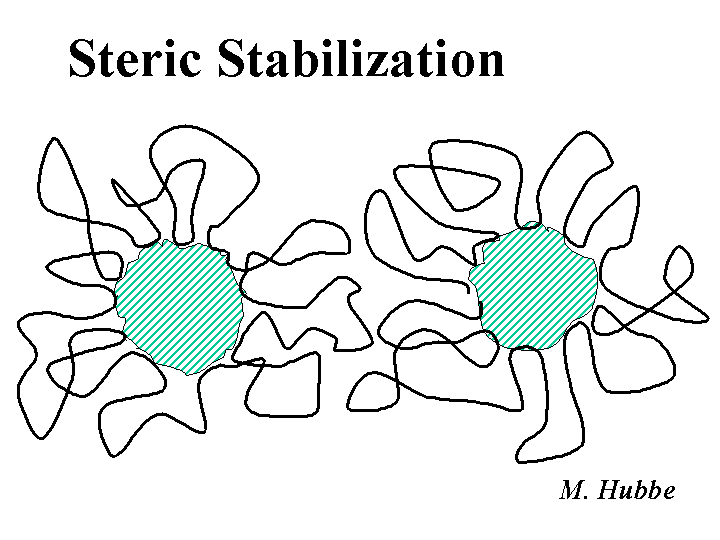
Streaming Current
The streaming current method is one of the most widely used means of detecting the endpoint of a charge demand titration. The mechanical parts of the device are very simple. A plastic piston moves up and down about four times per second within a closely-spaced plastic cylinder. Two electrode probes contact the solution near the closed bottom of the cylinder and at the top, where the cylinder widens out into a chamber. The piston motion causes a much more rapid reciprocal motion of aqueous fluid (the sample) within the annulus. The flowing liquid carries along any counter-ions that lie outside of the hydrodynamic slip plane at the plastic surfaces. The circuit of this current is completed and measured in an external connection and electronic device between the two electrode probes. During an evaluation of colloidal charge of an aqueous sample one adds an oppositely charged titrant until the signal goes to zero. In theory, this condition occurs when neutral complexes between the titrant and components of the sample become less soluble and cover the probe surfaces.
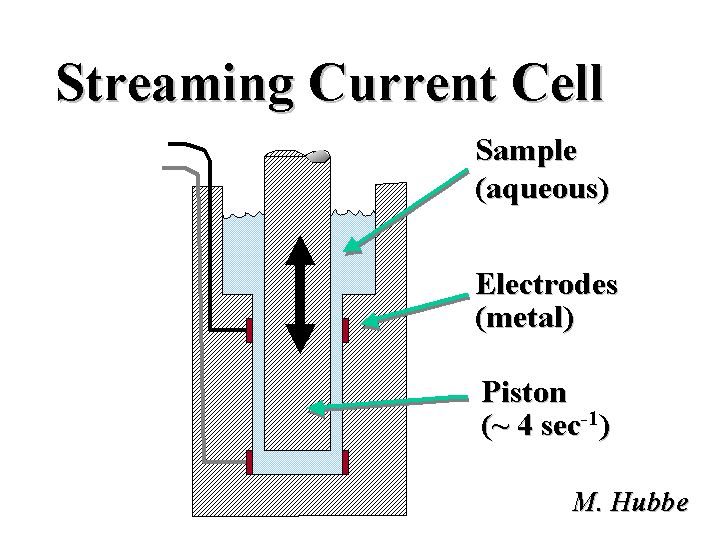
Streaming Potential
The streaming potential method is one way to determine the charged nature of fiber surfaces. The principle is similar to that of streaming current measurements, with a few subtle differences. Instead of plastic surfaces, the liquid flows through a pad of fibers from the sample itself. A known pressure is used to push the liquid. A resulting voltage is measured between electrode probes on either side of the pad. This voltage is then compared with the voltage at zero applied pressure. Streaming potential is related to zeta potential by factors that include the electrical conductivity, fluid viscosity, and the structure of the fiber pad. The value of streaming potential under given conditions of conductivity and pressure can be used to judge how strongly the furnish will interact with anionic or cationic additives. Better yet, one can titrate the streaming potential value to zero and get a very accurate measure of the cationic or anionic demand of the furnish.
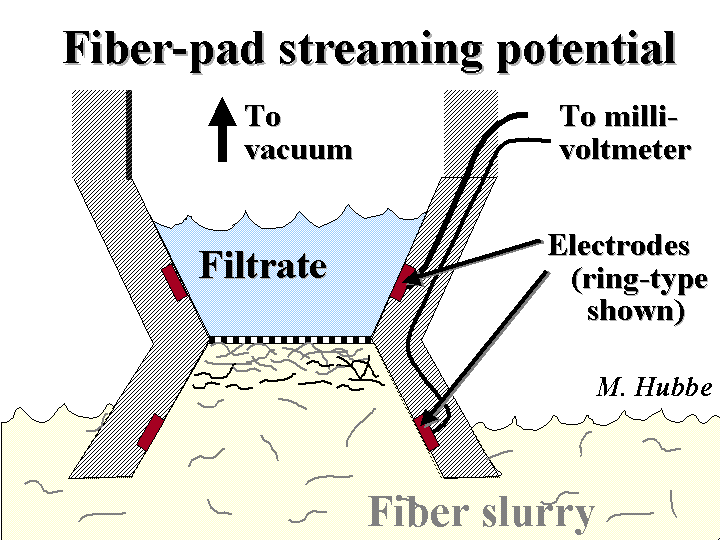
Surface-Active Agents or Surfactants
Surfactants are molecules having a dual character. Part of each molecule is hydrophilic. Part of each molecule is hydrophobic. The dual affinity means that surfactant molecules have a tendency to accumulate at interfaces between polar and nonpolar phases. Surfactants can help technologists to disperse emulsion particles, spread various liquids onto solids, and stabilize desirable foams. Surfactants can be a nuisance to papermakers when they stabilize undesirable foams, make it more difficult to hydrophobically size paper, hurt dry strength of paper, or hurt fine-particle retention. Rosin soap is a good example of a surfactant; another additive such as alum needs to be used in order to anchor rosin soap to furnish solids so that it can act as a sizing agent rather than as a surfactant. Surfactants are added intentionally to retention aid formulations, biocides, and various sizing agents to keep such products stable during storage.
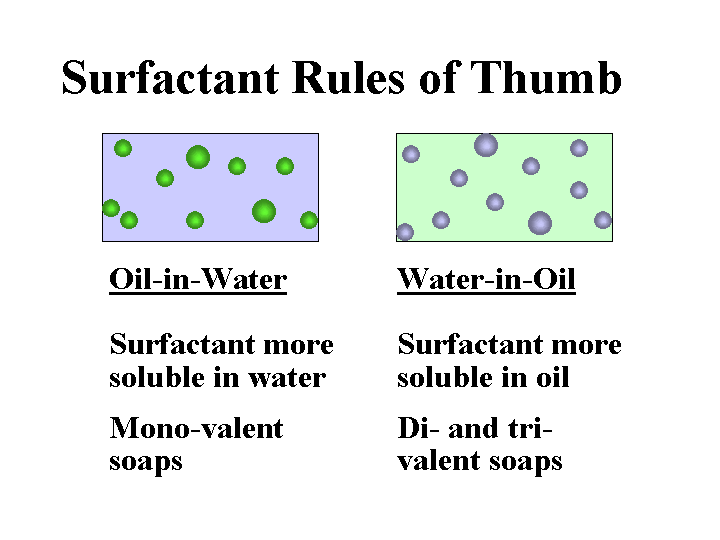
Total Acidity
The acidity or “total acidity” of an aqueous mixture equals the amount of strong base (such as NaOH) required to raise the pH of a unit volume or mass of sample to a value of 8.3. In general we cannot estimate a sample’s total acidity by knowing its pH. Mixtures that contain weak acids such as alum tend to have high values of total acidity.
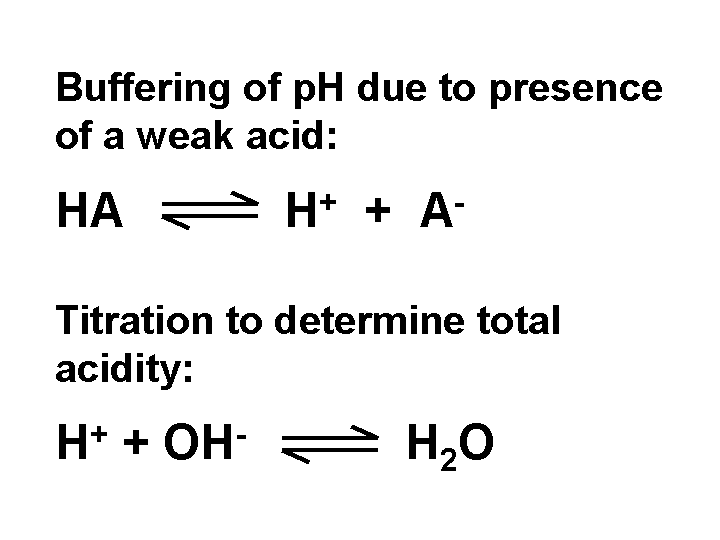
Water Retention Value
The water retention value (WRV) test provides an indication of fibers’ ability to take up water and swell. The WRV is also highly correlated to the bonding ability of kraft fibers. The test is carried out by placing a pad of moist fibers in a centrifuge tube that has a fritted glass filter at its base. The centrifuge is accelerated at 900g to remove water from the outside surfaces and lumens of the fiber (a higher force is used according to some European standards). The remaining water is believed to be associated with submicroscopic pores within the cell wall. The centrifuged fiber pad is weighed, dried at 105 degrees Centigrade, and then reweighed. The WRV value equals the ratio of the water mass to the dry mass. The WRV value of a papermaking furnish tends to increase with increasing refining and increasing pH. The WRV value tends to decrease when kraft fibers are dried and reslurried.
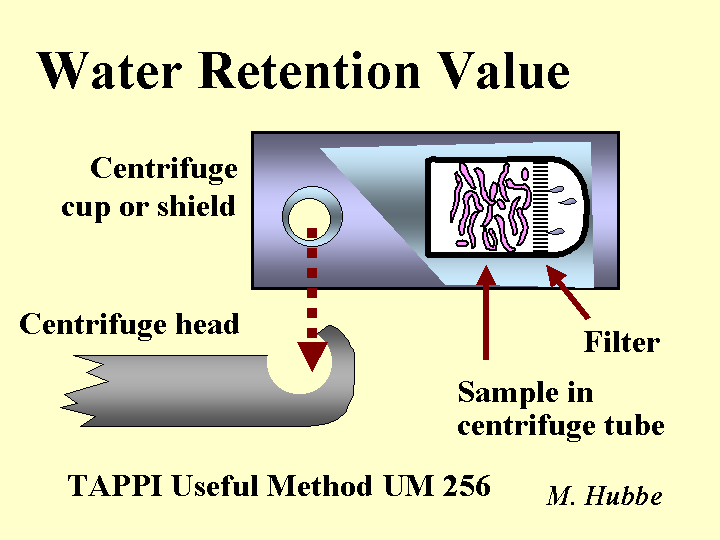
Wet End
The “wet end” of a paper machine is a general term for parts of the system that involve a slurry of fibers, fillers, and other additives. When looking at a paper machine it is easy to identify the “dry end” where a roll of paper is being formed. The rough dividing line between the wet end and the dry end is often drawn at the wet-press section, the last place in which water is pulled from the wet web of paper. One exception to this rule is the size press; because size press treatments can be closely related to what happens in the wet end, it is common that both subjects be considered in the same book or course. The beginning of the wet end is even harder to define. As a practical matter it may make sense to draw the line at the main refiner system, since most papermaking chemicals are added after that point.
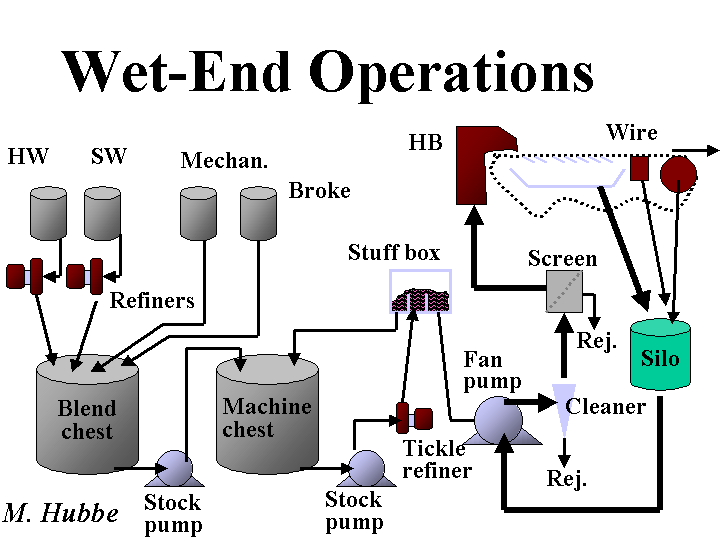
Wet Strength
The wet strength of paper is evaluated by taking a dry piece of paper, wetting it with a standard test fluid for a set amount of time, and then measuring the strength. The burst test is often used because of the ease and speed of testing. Wet tensile tests are also common, depending on the type of paper grade. One of the rules of thumb that papermakers use to evaluate wet strength is the ratio of wet strength to dry strength, e.g. the “percent wet over dry.” A true wet-strength paper grade has been defined by various writers to have a wet strength that is at least 10% or 15% of its dry strength. Wet strength can be achieved by treating the furnish with a reactive polymeric material such as polyamidoamine-epichlorohydrin (PAAE, for alkaline papermaking), melamine-formaldehyde or urea formaldehyde resins (MF or UF for acidic papermaking), or glyoxylated polyacrylamide for temporary wet-strength of some tissue products.
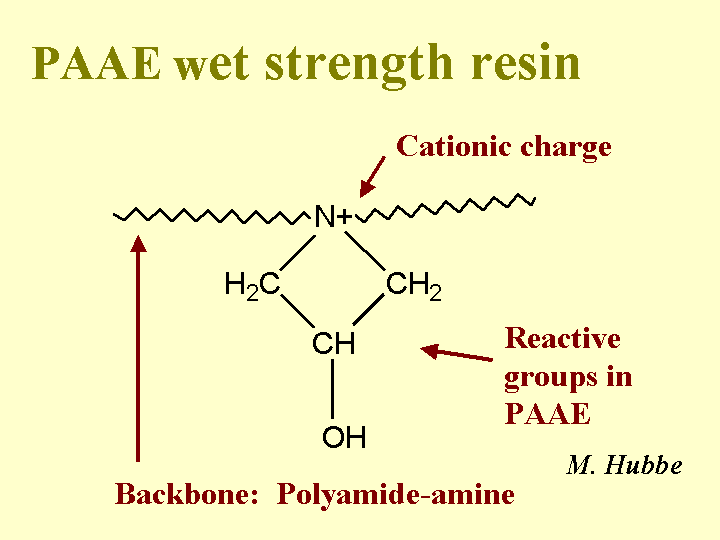
Wet-Web Strength
Before the paper is ever dried, it already has some strength. The strength of a partly-dewatered or wet-pressed sheet is called “wet-web strength” or “green strength.” This characteristic has nothing to do with wet strength. Rather, wet-web strength is dependent on such factors as fiber length, the coefficient of friction between adjacent moist fibers, and capillary forces in the liquid meniscus between two fibers. Wet-web strength can be increased by increasing the relative amount of softwood fibers, by more effective wet-pressing, and by decreasing the level of surface-active agents in the furnish. Paper with high wet-web tensile strength at a given solids level tends to run faster and with fewer web breaks on paper machines that have open draws before or within the wet-press section. Sometimes the best predictor of runnability is the relationship between wet-web tensile strength and the percent stretch to breakage.
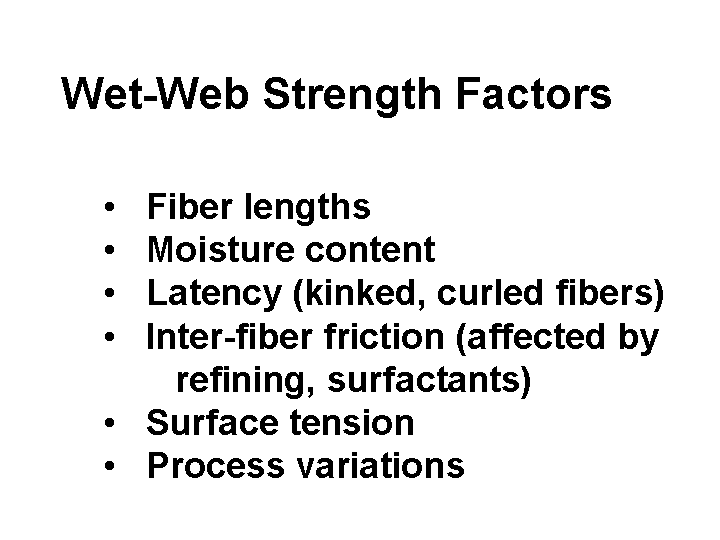
White Water
White water is a term papermakers use for process water that is removed from the furnish during formation of the sheet. The water appears white in many cases due to the presence of fiber fines, filler, and air bubbles that scatter light. Even if the process water appears brown, orange, or blue, due to the presence of black liquor, dyes, etc., it is still called white water. Most white water is reused within several seconds or minutes for the dilution of thick stock at a fan pump. Experience has shown that a paper machine system runs more efficiently and produces a more uniform product if the composition of white water is stable over time. This can be accomplished by monitoring the white water solids and controlling the flow of a retention aid. Excess white water is passed to a save-all, where solids are collected either by filtration or by flotation with air bubbles. The clear white water stream may be discharged to wastewater treatment, or it may be further filtered to make it suitable for use in showers on the paper machine. The air content of white water is kept to a moderate level by the design of a “tray” and “silo.” These structures allows bubble of air time to rise to the water surface. A deculator system can be used to remove more air just before the sheet is formed.
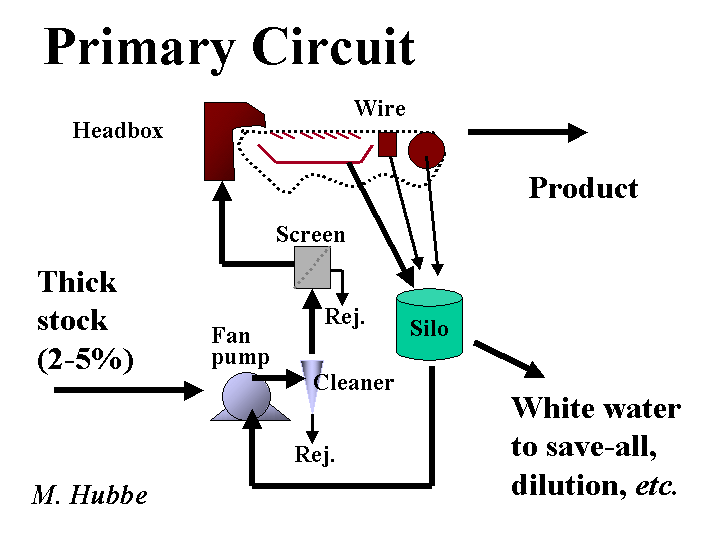
Zeta Potential
The zeta potential is defined as the average electrical potential at a hydrodynamic slip plane adjacent to a solid surface exposed to a liquid. Zeta potential data provide the papermaker with a way to predict how a furnish is likely to respond to the addition of cationic or anionic additives. A furnish having a zeta potential near to zero is more likely to drain well, especially if the drainage mechanism is dominated by additives having low molecular mass. Slurries of mineral fillers, sizing emulsions, etc., that have high absolute values of zeta potentials (say greater than plus or minus 20 mV) are likely to remain in stable dispersion during storage. Microelectrophoresis is the most common way that papermakers evaluate the zeta potential of fiber fines and fillers. Commercially available fiber-pad streaming potential devices often output a nominal “zeta potential,” but it is important to keep in mind that such output is not expected to agree with results from microelectrophoresis. The zeta potential is a good predictor of the magnitude of electrical repulsive forces between particles of known size and shape as a function of distance.
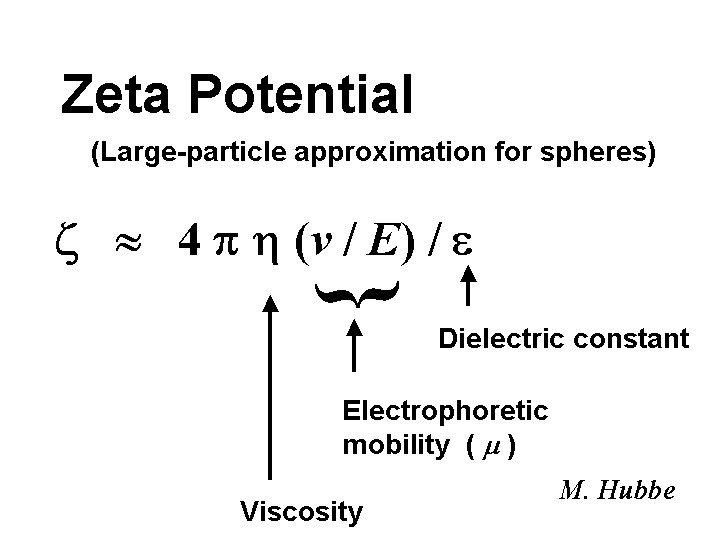